Статья — Какие радиаторы отопления выбрать
Радиаторы отопления
В процессе ремонта квартир, нового строительства, при монтаже системы отопления, многие сталкиваются с вопросом выбора радиаторов отопления.
Какие же основные виды радиаторов отопления представлены на рынке?
Рассмотрим наиболее популярные типы.
Алюминиевые радиаторы.
Сочетающие в себе хорошую тепловую инерцию и высокую теплопроводность, являются наиболее экономически выгодными, но имеют ряд недостатков.
Алюминий, являясь химически активным материалом, очень чувствителен к качеству теплоносителя используемого в системе отопления. Применение данных радиаторов обуславливает постоянный контроль качества воды.
Также, во избежание электрохимической коррозии, рекомендуется использовать переходники, изготовленные из чугуна или латуни.
Чугунные радиаторы.
Наиболее распространенные в ушедшем веке чугунные радиаторы имеют высокую теплопроводность и наибольшую устойчивость к некачественной воде в системе отопления.
К недостаткам можно отнести большой вес и неприглядный вид (хотя существуют дорогие модели с оригинальным дизайном), а также хрупкость материала и, как следствие, опасность разрушения вследствие гидравлических ударов.
Биметаллические радиаторы.
Биметаллические радиаторы получили свое название из за своего состава. Они состоят из нескольких, как правило двух металлов. Биметаллические радиаторы способны выдерживать высокое давление поэтому их обычно покупают и устанавливают в современных домах. Изначально биметаллические радиаторы были разработаны для применения в высотных домах с повышенным давлением. Они хорошо выдерживают агрессивную среду в центральных системах отопления.
Коллектор таких радиаторов может быть выполнен из стали, оснащенной алюминиевым профилем.
Изделие имеет очень высокие прочностные характеристики (способны выдержать гидравлические удары около 60 атм).
Стальные радиаторы.
По праву являются самым распространенным видом радиаторов в настоящее время.
Хорошая теплоотдача, устойчивость к перепадам давления в системе. Их неоспоримое преимущество – низкая цена, обеспечивают стальным радиаторам устойчивое положение на рынке.
Среди недостатков наиболее значимыми являются: низкая устойчивость к коррозии.
Это делает невозможным применение данных радиаторов в открытых системах отопления. Также наличие сварочных швов является слабым звеном в изделии. Именно они являются причиной большинства порывов и трещин в системе.
При строительстве коттеджей и реконструкции в квартирах с индивидуальным контуром отопления, можно использовать любой тип радиаторов. Необходимо лишь учитывать их технические нюансы.
При монтаже в многоэтажном доме рекомендуется уделить внимание более устойчивым к разрушающим факторам моделям.
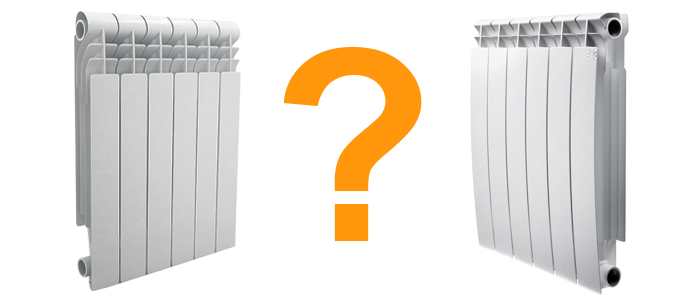
В процессе ремонта квартир, нового строительства, при монтаже системы отопления, многие сталкиваются с вопросом выбора радиаторов отопления.
Поделиться
Какой радиатор лучше алюминиевый или биметаллический
Алюминиевые радиаторы
Алюминиевые секционные радиаторы с успехом используются в отопительных системах жилых, общественных и промышленных зданий, а также в коттеджном строительстве.
Изготовление алюминиевых секционных радиаторов осуществляется методом литья под давлением. Обратите внимание на расположение лепестков примыкающих к вертикальному каналу алюминиевого радиатора: чем их больше, тем выше теплоотдача. Именно такое расположение идеально с точки зрения получения максимальной теплоотдачи. Кроме того, широкие и толстые лепестки обеспечивают большую теплоотдачу.
Толстые стенки вертикального коллектора говорят о высокой надежности устройства. Приборы отопления имеют современный дизайн и эстетичный вид. Поверхность покрыта белоснежной краской, которая не выцветает со временем.
Преимущества алюминиевых радиаторов
Алюминиевые радиаторы гораздо легче устаревших чугунных и стальных панельных радиаторов, что значительно облегчает их транспортировку и монтаж.
В опасные связи с теплоносителем могут вступить и алюминиевые батареи. Вода, которая циркулирует по трубам содержит различные примеси, они вступают в химическую реакцию с металлом в результате которой в батарее образуется воздух. Со временем давление увеличивается и это может привести к разрыву алюминиевой конструкции.
Биметаллические радиаторы
Специалисты считают, что по совокупности показателей биметалл оптимален для экстремальных российских условий.
Конструкция биметаллических радиаторов
Каркас должен состоять из двух слоев:
- внутренний из нержавеющей стали;
- внешний из теплопроводного алюминия.
Такая конструкция способна выдерживать давление до 40 атмосфер, но проверьте — стальным должен быть не только вертикальный канал но и коллектор.
Стальной сердечник усиливает конструкцию этих приборов. Благодаря ему они выдерживают высокое давление характерное для российской практики. Вдобавок, стальная начинка спокойнее других реагирует на щелочность воды (водородный показатель pH).
Виды биметаллических радиаторов
Биметаллические радиаторы бывают секционными и блочными. Секция — минимальная неразборная единица радиатора, а блок состоит из 2-3 или 4 колонок, которые также не разбираются. Она выглядит как соединенные между собой секции.
Чтобы подобрать радиатор необходимой мощности, вы набираете соответствующее число секций или комбинируете блоки в соответствии с тем, на насколько мощный радиатор вам требуется. В упрощенном виде одна секция радиаторы на два квадратных метра.
Как установить радиатор
Перед покупкой радиаторов необходимо замерить высоту подоконников квартиры. От этого будет зависеть размер. Стандартных размеров два: 35 и 50 сантиметров. При этом учтите, что расстояние между нижним ребром радиатора и поверхностью пола должна быть не менее 10 сантиметров. Такое же расстояние должно быть между радиатором и подоконником, а расстояние между задней стенкой радиатора и стеной должно быть не менее 3 сантиметров.
Подшипники — журнал Engine Builder
Проектирование и разработка подшипников двигателей стали более важными в стремлении к повышению эффективности и производительности. (Фото из ACL)Подшипники двигателя выполняют тяжелую работу для такого маленького компонента. Они должны выдерживать большие нагрузки на тонкой масляной пленке (толщиной от 0,0001 до 0,0004 мкм) между собой и шейками коленчатого вала, чтобы предотвратить контакт металла с металлом.
Одной из основных причин выхода подшипников из строя являются грязь и мусор, которые попадают в масляный поддон и засасываются между поверхностью подшипника и коленчатым валом, разрывая тонкую масляную пленку и создавая контакт металл-металл. С этого момента различные применения в двигателе и материалы подшипников могут реагировать по-разному, но конечный результат, как правило, один и тот же — затертый подшипник. А этого не хочет ни один производитель двигателей или подшипников.
Мы поговорили с производителями подшипников, чтобы узнать, в каком направлении движется технология в отношении материалов и конструкции подшипников, а также как производители двигателей могут лучше понять, какие подшипники использовать в конкретных условиях.
«По мере развития двигателей термины «дизайн» и «производство» становятся все более важными, — говорит Майк Скотт из ACL Bearings. «Это в основном обусловлено повышением эффективности двигателя, что приводит к более высоким нагрузкам на подшипники и более высоким рабочим температурам подшипников при использовании смазочных масел с более низкой вязкостью».
В результате, по словам Скотта, в целом уменьшилась толщина масляной пленки между шейкой и подшипником. «Поскольку минимальная толщина масляной пленки может быть менее 0,0004 мкм, форма (конструкция) и точность изготовления являются ключевыми факторами, способствующими образованию стабильной масляной пленки и обеспечению разделения вала и подшипника при любых условиях эксплуатации», — объясняет он.
Несмотря на то, что качественные подшипники обладают неотъемлемыми свойствами, которые компенсируют некоторую степень несоосности (то, что инженеры по подшипникам называют прилегаемостью) и обеспечивают защиту от твердых загрязнений в масле (встраивание), производители двигателей могут многое сделать для обеспечения долговечности подшипников, внимание к подготовке коленчатого вала и общей чистоте сборки. На самом деле, значительный процент отказов подшипников можно отнести непосредственно к процессу сборки, поэтому рекомендуется поддерживать его как можно более чистым.
«Самое главное для установщиков — это чистота при сборке, — говорит Боб Стерк из Federal Mogul. «Все должно быть максимально безупречно. Грязь – убийца подшипников номер один. Когда у нас случаются сбои, это всегда, в подавляющем большинстве случаев, из-за мусора и въевшейся грязи.
Вторя словам Стурка по чистоте, Бретт Дайрингер из MAHLE Clevite говорит, что тщательная очистка блока после механической обработки — лучший способ предотвратить попадание грязи и мусора в масляную систему после ремонта.
«Использование горячей мыльной воды и хорошего набора щетинных щеток — лучший способ очистки блоков цилиндров, коленчатых валов и других деталей двигателя перед сборкой двигателя», — говорит Дайрингер. «Помните, что любой мусор, оставшийся после восстановления, будет подхвачен масляной системой и попадет в подшипники».
Еще одно важное соображение при работе с подшипниками двигателя, на которое следует обратить внимание, заключается в том, что размеры стенок должны быть одинаковыми, чтобы вы могли устанавливать зазоры без необходимости проходить и измерять несколько подшипников для правильной посадки.
С точки зрения производителя, компания King’s Ron Sledge признает, что размеры подшипников и материалы, соответствующие применению, очень важны для установщика и конечного пользователя. «Установщику нужны очень стабильные размеры несущей стены, чтобы легко ориентироваться на желаемый зазор», — говорит Следж. «Его кривошипы имеют одинаковый размер, поэтому он хочет, чтобы подшипники также имели одинаковые размеры. Он также может сэкономить время и деньги, поскольку ему не нужно измерять различные вкладыши подшипников, чтобы выбрать правильный для достижения требуемого зазора».
Скотт из ACL говорит, что решение его компании, аналогичное решению King, заключалось в повышении точности производственного процесса. «У нас есть портфолио подшипниковых материалов с проверенной надежностью для различных двигателей», — говорит он.
Скотт продолжает: «Это дает производителю двигателей базовую уверенность в эксплуатационных возможностях. Повышенная точность, особенно в отношении толщины стенки подшипника, обеспечивает дополнительную уверенность в том, что будут достигнуты оптимизированные зазоры в подшипниках, что приведет к: оптимизированному образованию масляной пленки высокого давления для лучшей поддержки нагрузки; повышенная износостойкость; более предсказуемое давление масла и скорость потока для обеспечения постоянной подачи по всему двигателю; и адекватное охлаждение подшипников при любых условиях эксплуатации».
Материалы имеют значение
Выбор правильного материала подшипника имеет жизненно важное значение для бесперебойной работы в любом приложении. Наиболее часто используемые материалы для подшипников коленчатого вала — алюминий, медь, свинец и олово. Очевидно, есть и другие, говорят эксперты, но это основные элементы, которые используются. И все они, в сравнении, намного мягче, чем железные и стальные коленчатые валы, которые работают против них.
«Материалы подшипников должны удовлетворять множеству различных условий в двигателе, включая нагрузку, возможность заделки и устойчивость к заеданию, и это лишь некоторые из препятствий, которые они должны преодолевать», — говорит Следж.
К счастью, говорят производители, годы исследований и испытаний позволили разработать различные материалы для самых разных целей, от использования в уличных условиях до сверхвысоких эксплуатационных характеристик для оптимизации работы подшипников на вторичном рынке.
Как известно большинству производителей двигателей, в современных двигателях (конца 90-х годов и новее) используются биметаллические алюминиевые подшипники, но у каждого производителя есть свой собственный рецепт конструкции и характеристик, которые им нужны. Базовая конструкция представляет собой стальную заднюю часть со слоем силикона-алюминия, обращенным к коленчатому валу.
По словам Мэтта Баркхауса из Federal-Mogul, если вы занимаетесь капитальным ремонтом, очень просто выбрать правильный подшипник из каталога, в котором перечислены все спецификации и доступные размеры.
Баркхаус говорит, что на их биметаллических подшипниках внутренний диаметр просверлен, поэтому мусор вымывается, а не застревает. «Это одно из его реальных преимуществ», — говорит он. «Другое преимущество биметалла — износостойкость. Они прослужат практически вечно, если вы регулярно меняете масло и двигатель работает в довольно нормальном рабочем состоянии».
Алюминиевые подшипники могут служить намного дольше при умеренных нагрузках из-за износоустойчивости и твердости силиконового композита, который фактически полирует коленчатый вал и вытирает любые узлы или мусор с пути или вымывает его, продолжает Баркхаус.
«Производители комплексного оборудования перешли на биметаллические подшипники, потому что они не содержат свинца, экономичны в производстве и очень прочны, что позволяет им очень долго работать в легковых автомобилях», — говорит Дайрингер из MAHLE Clevite. «Как мы все видели, современные двигатели нередко проезжают 150 000 миль и более на оригинальных подшипниках».
Практически все рабочие подшипники сегодня изготавливаются из трех металлов. Триметаллические подшипники имеют такую же стальную заднюю часть, как и биметаллические подшипники, медно-свинцовый промежуточный слой и поверхностный слой из мягкого материала, такого как Babbit
. более щадящий, что обеспечивает лучшую встраиваемость, чем более твердый биметаллический подшипник», — говорит Дайрингер.
Материалы подшипников в некотором роде являются скрытым секретом конструкции подшипников, по мнению наших экспертов. «Скрытый» аспект способности материала подшипника заключается в разработке металлургических свойств, воплощенных в сплавах. Таким образом, хотя все триметаллы и все биметаллы могут выглядеть одинаково, их свойства и способности могут существенно различаться.
«В то время как правильная установка обеспечивает основу для работы подшипниковой системы, материалы обеспечивают основу для долговечности системы», — говорит Скотт из ACL. «Для успешной работы подшипникам требуется ряд характеристик, которые, с точки зрения свойств материала, требуют определенного компромисса. Например, прочность, необходимая для передачи высоких циклических нагрузок, должна быть умеренной, чтобы обеспечить хорошую устойчивость к заеданию. Способ достижения этого баланса зависит от комбинации материала и сплава каждого подшипника. Наиболее ярким примером является сравнение свойств «биметаллов» на основе алюминия и «триметаллов» на основе меди и свинца».
Каковы основные различия в твердости, прочности и возможности заделки между современными подшипниками из алюминия и триметалла?
«Обычно алюминиевые подшипники обеспечивают лучшую встраиваемость и прилегаемость, в то время как подшипники из триметалла обеспечивают большую усталостную прочность и твердость», — говорит Следж. «Слой алюминиевого сплава поверх стальной спинки имеет толщину не менее 0,012? толстый и может включать частицы крупнее 0,0005? в диам. Толщина наплавки на трехметаллических подшипниках варьируется от 0,0005° до 0,0008 мкм. поэтому допускает меньшую встраиваемость ».
Стурк из Federal-Mogul говорит, что существуют основные различия в твердости двух подшипников, а также некоторые другие различия в прочности и возможности заделки. «На мой взгляд, встраиваемость не такая уж большая проблема. Я думаю, что современные алюминиевые биметаллические подшипники могут справиться с разумным количеством мусора. Но если их избыточное количество, то лучше триметаллические подшипники. Возможность встраивания над плитой позволяет им немного лучше справляться с мусором. Если это разумное количество, если за маслом ухаживали должным образом, я не особо беспокоюсь о возможности заливки алюминия».
Если вы хотите получить больше энергии, эксперты говорят, что медно-свинцовые подшипники, вероятно, являются оптимальным выбором. Стерк объясняет, что инженеры по подшипникам в первую очередь заботятся об удельной нагрузке, а не о количестве лошадиных сил, чтобы оценить прочность конкретного подшипника или материала. Единичные нагрузки возникают из-за давления в цилиндре, которое создается над подшипниками в камере сгорания.
Изготовителю двигателя трудно оценить давление сгорания без большого количества дорогостоящего испытательного оборудования, которое было бы у OEM-производителя или производителя подшипников, поэтому Стурк говорит, что, вероятно, лучше использовать триметаллический подшипник для любого обновления, просто чтобы быть в безопасности .
По словам экспертов, существует большая разница в степени износа подшипников из триметаллов меди/свинца и биметаллических подшипников из алюминия.
Триметаллические подшипники из медно-свинцового сплава по-прежнему являются самыми прочными материалами, доступными сегодня, говорит Стерк. Он говорит, что если вы модернизируете или добавляете нагнетатель или используете другие методы для извлечения большей мощности, это обычно увеличивает нагрузку на подшипники. «В таком случае, — говорит он, — триметаллические подшипники будут выдерживать гораздо более высокие нагрузки. Наши материалы h24 (медь/свинец) выдерживают единичные нагрузки до 15 000 фунтов на квадратный дюйм. Алюминий выдержит намного меньше, около 8000-9.,000 фунтов на квадратный дюйм. Это большая разница в прочностных характеристиках», — отмечает он.
По данным Dayringer, в гоночных двигателях наблюдается больший прогиб коленчатого вала, деформация отверстия корпуса штока и меньшая толщина масляной пленки по сравнению с двигателями легковых автомобилей, и поэтому для них требуются другие материалы и конструкция, чем для биметаллических алюминиевых подшипников. «Более мягкое баббитовое покрытие позволяет поверхности подшипника слегка «двигаться» вместе с коленчатым валом, чтобы избежать заклинивания при высоких нагрузках и оборотах, что делает триметаллические подшипники предпочтительным выбором для двигателей с высокими характеристиками и для гоночных двигателей», — объясняет он.
Свойства, которыми должен обладать подшипник, можно сравнить с натянутым канатом, потому что, с одной стороны, вам нужны компоненты твердой усталостной прочности для долговечности и грузоподъемности, а с другой стороны, вам нужны характеристики мягкой фазы для прилегания (когда вещи вне выравнивания), встраиваемость и свойства скольжения. Когда производители выбирают материал подшипника, они смотрят на область применения двигателя и пытаются определить самое важное, что нужно двигателю, а затем проектируют подшипник исходя из этого.
Современные биметаллы содержат смесь других материалов, таких как кремний, который представляет собой твердую частицу, добавленную для увеличения срока службы. У них есть олово, которое считается металлом с мягкой поверхностью, которое обеспечивает возможность встраивания и прилегания, поэтому современные алюминиевые биметаллы содержат легирующие элементы для решения этих проблем. Но все же не все сплавы одинаковы.
Хотя все триметаллы и все биметаллы могут выглядеть одинаково, их свойства и способности могут существенно различаться. Способность материала подшипника находится в «скрытой» части конструкции металлургических свойств, воплощенных в сплавах.
«Различия сводятся к составу сплава, условиям литья, методам склеивания и термообработке биметаллов, — говорит Скотт. «А для триметаллов любые различия объясняются составом сплава, условиями спекания/литья и технологиями гальванического покрытия/покрытия».
Все эти факторы дают производителям подшипников большую свободу выбора материалов, и производители двигателей могут запутаться, пытаясь понять, насколько материалы подходят для их конкретного применения. Поскольку качество материала может быть неочевидным, производителям двигателей также трудно сделать выбор между конкурирующими продуктами.
Материалы разных поставщиков ведут себя по-разному, и в каждом семействе материалов существует значительный диапазон возможностей. Восстановителю почти невозможно судить по номинальной стоимости, как подшипник какой-либо марки будет работать в широком диапазоне характеристик, поэтому эксперты говорят, что лучше всего полагаться на подшипники известных, известных брендов.
Когда подшипники обнаруживаются поврежденными или имеют необычный или неравномерный износ, это обычно указывает на другие проблемы, требующие исправления, проблемы, которые, если их не устранить, могут привести к той же участи замененных подшипников.
Особая благодарность компаниям MAHLE Clevite, King Engine Bearings, ACL и Federal-Mogul за их вклад в подготовку этой статьи.
Как выбрать лучшее полотно для сабельной пилы
Сабельные пилы являются одним из самых универсальных инструментов. Частично эта универсальность обусловлена огромным набором лезвий, доступных для резки самых разных материалов. С правильным диском ваша пила может резать дерево, гвозди, стекловолокно, ветки, штукатурку, кирпичную кладку и металлы, включая алюминий, чугун, сталь и даже высокопрочные сплавы. Но как выбрать правильный диск для материала, который нужно разрезать?
Есть много характеристик лезвия, которые следует учитывать. Как правило, это включает в себя материал лезвия, длину, ширину, толщину и количество зубьев на дюйм (TPI). Для конкретных типов резки можно выбрать форму лезвия, форму зуба, ширину пропила, впадину и рисунок зуба. Несмотря на то, что есть много вариантов, выбрать правильный диск для сабельной пилы легко, если вы знаете основы.
Материал лезвия
Высокоуглеродистая сталь (HCS)
Лезвия из углеродистой стали — самый недорогой тип, а также самый распространенный. Они являются самым мягким из материалов лезвия и, как правило, более гибкими, что позволяет сгибать их, не ломая при правильном применении. Это также делает их наименее долговечными. Они хороши для резки мягкой древесины, ДСП и пластика. Однако они быстро тускнеют при работе с твердыми породами дерева, металлом и другими твердыми материалами.
Быстрорежущая сталь (HSS)
Лезвия из быстрорежущей стали подвергаются процессу закалки, что делает их более термостойкими и долговечными, чем их аналоги из углеродистой стали. Они служат до 5 раз дольше, чем углеродистая сталь. Эта твердость делает их менее гибкими и, следовательно, более склонными к поломке при сгибании. Это также позволяет им резать твердую древесину, алюминий и цветной металл без чрезмерного износа, затупления и поломки зубьев.
Биметалл
Биметаллические лезвия сочетают в себе корпус из высокоуглеродистой стали для гибкости и устойчивости к излому, а также зубья из быстрорежущей стали для термостойкости, твердости и долговечности. В среднем лезвия из биметалла служат в 10 раз дольше, чем лезвия из углеродистой стали. Хотя их стоимость немного выше, чем у лезвий из быстрорежущей стали или быстрорежущей стали, они обеспечивают универсальность и прочность для более требовательных применений. Это делает их наиболее популярным типом лезвий среди людей, занятых в торговле, автомобильных мастерских и других профессиях, где пилорамы используются часто или ежедневно. Мы также рекомендуем биметаллические лезвия для самостоятельных работ и периодического использования из-за их долговечности и долговечности.
В других биметаллических лезвиях используется режущая кромка из сплава кобальтовой стали.
Купить биметаллические лезвия
С твердосплавным наконечником
Пильные полотна с твердосплавными наконечниками также являются биметаллическими полотнами, но с наконечником из карбида (карбида вольфрама или карбида титана) на конце каждого зуба. Эти карбидные материалы чрезвычайно твердые, термостойкие и ударопрочные. Они также предлагают в 20 раз больший срок службы по сравнению со стандартным биметаллическим лезвием. Может резать более толстые куски металла, включая чугун, нержавеющую сталь и высокопрочные сплавы. Это делает их идеальными для резки металлов, которые почти сразу же разрушили бы лезвия из HCS, HSS или традиционных биметаллических дисков, таких как болты класса 8 и автомобильные стойки, армированные бором.
Купить лезвия с твердосплавными напайками
Твердосплавный песок
Лезвия из карбида (обычно из карбида вольфрама) не имеют зубьев, как традиционные пилы. У них есть абразивная полоса, которая используется для резки плотных материалов, таких как керамическая плитка, цемент, кирпич, мрамор, другой камень и кирпичная кладка, более твердые металлы, такие как чугун и стекловолокно. Твердость карбидного зерна позволяет резать эти материалы, не повреждая их и не изнашивая преждевременно.
Алмаз
Алмазные диски также являются абразивными, но вместо карбида в них используются алмазы. Это самые дорогие полотна для сабельных пил. Они используются для резки бетона, стекла, стекловолокна и керамики, а также для резки фиброцемента, чугуна и кирпичной кладки. Твердость алмаза и тонкость абразивного зерна необходимы для резки хрупкого материала, такого как стекло (которое может быть разрушено зубчатым лезвием), и очень твердого и плотного материала, такого как бетон (который разрушит зубчатое лезвие).
Профессиональный наконечник:
При выборе лезвия помните следующее практическое правило: режущая кромка лезвия должна быть тверже, чем материал, который вы режете.
Длина
Длина полотна сабельной пилы варьируется от 3 до 12 дюймов. Стандартные длины: 4, 6, 8, 9 и 12 дюймов, наиболее часто продаются 6 и 9 дюймов. Короткие лезвия более жесткие и поэтому более агрессивные. Эта жесткость обеспечивает более прямой и квадратный срез, что делает их идеальными для погружной резки, медных труб и более тонких металлов. Более длинные лезвия более гибкие и могут рассеивать больше тепла, поскольку имеют большую площадь поверхности. Такие работы, как снос, обрезка, автоматический демонтаж и спасательные работы, требуют более длинного лезвия. Эта гибкость также позволяет сгибать лезвие, когда требуется ровный срез.
Длина лезвия, которую вы выбираете, всегда должна быть немного больше, чем толщина материала, который вы режете. Это уменьшает скольжение и заедание и дает вам некоторую свободу движений. Если вы возьмете слишком длинное лезвие, конец может качаться, иногда сильно. Это вызывает сильную вибрацию, замедляющую резку, и в конечном итоге может повредить вашу работу и привести к искривлению лезвия.
Профессиональный наконечник:
Длина лезвия всегда должна быть на 2–3 дюйма больше, чем ширина разрезаемого материала.
Ширина и форма
Широкие лезвия обеспечивают большую устойчивость. Они устойчивы к изгибу и вибрации, обеспечивая более прямые и агрессивные разрезы. Эта дополнительная поддержка делает более широкие лезвия более подходящими для тяжелых условий эксплуатации, таких как снос (древесина с гвоздями), автоматический демонтаж, а также пожарно-спасательные работы. 3/4″ — 1″ считаются широкими лезвиями.
Лезвия с меньшей шириной обеспечивают большую гибкость для общего использования или более тонкой резки. Обычно они находятся в диапазоне от 1/2 до 3/4 дюймов. Очень малая ширина имеет толщину менее 1/2 дюйма и обычно используется для резки завитков — изогнутых форм и деталей из дерева, металла и пластика.
Форма лезвия также имеет значение. Лезвия с наклонной формой лучше подходят для погружной резки. Прямые лезвия предназначены для резки кромок. Многие лезвия имеют зазубренный или наклонный кончик или полусужающуюся заднюю часть, чтобы они могли адекватно выполнять обе задачи.
Толщина
Стандартная толщина полотна для сабельной пилы:
- 0,035″ — стандартный режим
- 0,042″ — для средних и тяжелых условий эксплуатации
- 0,050″ — для тяжелых условий эксплуатации
- 0,062 дюйма — для сверхтяжелых условий эксплуатации
Более толстые лезвия более долговечны и устойчивы к изгибу и вибрации. Они также допускают большее давление подачи для более тяжелых работ. Сверхпрочные материалы толщиной от 0,050 до 0,062 дюйма лучше всего подходят для сноса древесины с гвоздями, автоматического демонтажа, пожарно-спасательных работ и резки более толстых или плотных металлов. Лопасти для тяжелых условий эксплуатации жесткие и имеют большую
ширина пропила, поэтому они не рекомендуются для приложений, где требуется точная резка или гибкость.
Лезвия общего назначения обычно имеют диаметр 0,035 дюйма и подходят для большинства применений. Они более гибкие и обеспечивают более быструю резку. Они также обычно дешевле, поскольку в их конструкции используется меньше материала.
Профессиональный наконечник:
Длинные лезвия легче гнутся. Если это нежелательно в вашем приложении, рассмотрите более толстое лезвие для длины 6 дюймов или больше.
Число зубьев на дюйм (TPI)
Диски для сабельных пил варьируются от 3 до 24 TPI. Количество зубьев на дюйм определяет скорость и шероховатость реза.
Лезвия с более низким TPI режут быстро, но оставляют более грубые края. Лезвия в диапазоне от 3 до 11 TPI обычно лучше всего подходят для
деревообрабатывающие и демонтажные работы. Лезвия для обрезки, как правило, находятся на низком уровне, а лезвия для сноса / поедания гвоздей, как правило, составляют около 8-11 TPI.