Опрессовка и вакуумирование системы кондиционирования ЦОД: как не допустить ошибок? Часть 1
На этапах монтажа, пусконаладки и ввода в эксплуатацию холодильной техники есть ряд скрытых работ. Их особенность в том, что допущенные в них ошибки проявляют себя не сразу. Система запустится и будет работать, но через какое-то время — это может быть как пара месяцев, так и 2-3 года — внезапно выйдет из строя, например, из-за утечки фреона или поломки компрессора.
В первую очередь речь идет о таких процессах, как опрессовка и вакуумирование. Они критически важны для надежной и долгой службы системы. Однако именно из-за того, что последствия отсрочены, к ним часто относятся недостаточно ответственно.
Как должны быть выполнены эти работы? Что нужно знать заказчику и что он может сделать, чтобы убедиться в их качестве и предотвратить потери? Мы подготовили практическую инструкцию по важным моментам, которые нужно учесть и проконтролировать.
Сегодня говорим о первом из этих процессов — опрессовке.
Зачем нужна опрессовка
Когда трасса смонтирована, ее нужно проверить на герметичность. Для этого выполняется опрессовка: внутри трассы создают избыточное давление и замеряют его через некоторое время. Если герметичность контура нарушена, давление в нем упадет. Таким образом можно обнаружить незаметные визуально микротрещины, через которые просачивается опрессовочный материал (в случае с холодильными системами — газ), а впоследствии будет выходить хладагент.
Если этот процесс провести неправильно, то можно пропустить течь. И уже после запуска система внезапно отключится из-за падения давления.
Как должна выполняться опрессовка
Опрессовка производится по определенному регламенту для холодильных систем. Для систем с разными хладагентами он может различаться. В общем виде последовательность действий выглядит так.
- Контур заполняют азотом. В зависимости от объема системы это может занять от 2-3 до 30 минут.
- После этого системе нужно дать 30-60 минут “постоять”, чтобы газ равномерно распределился.
- Проводят контрольный замер показаний. Его результаты фиксируют, затем отключают манометрическую станцию.
- Через сутки выполняют повторные замеры, которые покажут, есть ли падение давления.
Последний пункт особенно важен. Между замерами необходимо подождать достаточное время — в среднем около суток — чтобы получить достоверные результаты. Это требование часто не соблюдают и снимают показания уже через час-два, чтобы ускорить процесс.
Как избежать ошибок при опрессовке
При проведении опрессовки (как и других работ) важно соблюдать и технические требования, и регламент процедур. Но, пытаясь сэкономить время и ресурсы, подрядчики нередко нарушают и то, и другое. В результате, во-первых, через некоторое время техника внезапно выходит из строя. И во-вторых, оказывается сложно найти причины поломки и ответственных за нее.
На что обратить внимание заказчику? Основные контрольные точки.
- Каждый этап работ должен быть подтвержден актом.
Независимо от того, выполняют ли разные работы разные подрядчики или специалисты из одной компании — каждый этап должен быть передан с оформлением фиксирующих документов.
После монтажа выдается акт о том, что система смонтирована и готова к опрессовке. Следующий акт — о принятии результатов опрессовки и передаче на вакуумирование. В нем обязательно указывается остаточное давление в контуре.
Впоследствии, если в системе возникнут проблемы, это позволит быстрее найти причину.
- Заказчику (или его представителю) стоит лично присутствовать при опрессовке.
Если этого не сделать, то заказчик получит только готовый результат, не зная, как шел процесс. Если в будущем всплывут проблемы, связанные с ошибками опрессовки, у него не будет оснований предъявить претензии. К тому же присутствие заказчика само по себе снизит вероятность халатного отношения.
Личный визуальный контроль нужен на обоих этапах опрессовки. При заправке контура необходимо убедиться, что процедура проводится по измерительным приборам с нужным уровнем давления. При снятии показаний — проверить, выдержано ли нужное время, проконтролировать цифры и подтвердить, что в акт опрессовки внесены верные данные.
Кроме того, полезно заранее изучить регламент, по которому будет производиться опрессовка. Чтобы не разбирать техническую документацию и ГОСТы целиком, можно попросить организацию, ответственную за опрессовку, предоставить памятку с кратким описанием процесса и норм оценки показателей.
- Опрессовку нужно проводить азотом особой чистоты.
Фреоновые машины необходимо опрессовывать азотом особой чистоты, который имеет минимальное количество примесей и не содержит воды. Вода губительно сказывается на масле: в процессе трения образуется щелочь, которая разъедает обмотку компрессора и приводит к замыканию обмоток. Плюс к тому, вода не может смазывать цилиндры компрессора, что приводит к заклиниванию.
- Важно использовать электронную манометрическую станцию.
Сейчас такое оборудование доступно любой серьезной монтажной организации, а его использование значительно повышает качество работ. Устаревшие механические приборы имеют низкую точность — до 5 бар, которой недостаточно для определения показателей давления. Электронные станции определяют его с точностью до сотых долей единицы.
- Рекомендуется опрессовывать давлением с коэффициентом 1,25 от рабочего.
Система должна быть не только герметичной, но и прочной, чтобы не разорваться при высоких нагрузках. Поэтому, чтобы проверить ее запас прочности, по правилам опрессовку проводят давлением 1,25 от рабочего. Например, если максимальное давление в системе составляет 10 бар, то опрессовку проводят на 12,5 бар. Это гарантирует, что при максимальном давлении трубопровод не лопнет и система не потечет.
Правда, здесь есть нюанс. Если система имеет нестандартное рабочее давление (уже есть системы с показателями до 45 бар), то это правило соблюсти не всегда возможно. В таких случаях нужно ориентироваться на рекомендации по опрессовке от производителя.
- Опрессовку вакуумированием выполнять нельзя.
Иногда монтажные организации предлагают пропустить опрессовку как самостоятельный этап, проведя так называемую “опрессовку вакуумированием”. Предполагается, что если система хорошо держит вакуум — это само по себе подтверждает ее герметичность. Однако это в корне неверно.
После остановки вакуумного насоса давление в системе будет расти из-за постепенного выпаривания газов, которые содержатся в масле. Этот процесс скомпенсирует падение давления при утечке. Поэтому с помощью вакуумирования оценить герметичность контура невозможно.
Конечно, этим списком не исчерпываются все нюансы. Тем не менее, такой “обязательный минимум” значительно снизит вероятность сбоев в работе систем кондиционирования из-за некачественной опрессовки.
Вы можете проконтролировать все эти моменты самостоятельно, а если необходимо — всегда готовы помочь наши специалисты. Мы можем взять на себя как проведение этих работ, так и контроль за их выполнением.
Что дальше? После правильно выполненной опрессовки система передается на вакуумирование. К нему мы и перейдем в следующей статье.
Инертизация и опрессовка азотом трубопроводов и промышленного оборудования
Услуги ИНЕРТИЗАЦИЯ И ОПРЕССОВКА АЗОТОМ ПРОМЫШЛЕННОГО ОБОРУДОВАНИЯПромышленная химия
Химические реактивы и реагенты
Соли драгоценных металлов
ГСО и стандарт-титры
Лабораторная мебель и оборудование
Услуги для очистных сооружений и систем водоподготовки
- Поставка реагентов, сорбентов, расходных материалов
- Подбор технологического оборудования
- Обслуживание очистных сооружений и систем водоподготовки
- Сервис и ремонт оборудования
Производство растворов и смесей
Инертизация и опрессовка азотом промышленного оборудования
Логистические услуги
Спецпредложения
КЛЮЧЕВЫЕ НАПРАВЛЕНИЯ ДЕЯТЕЛЬНОСТИ НАШЕЙ КОМПАНИИ:
— Оптимизация цепи поставок по смешанным группам товаров (комплексный поставщик)
— Проектирование и монтаж криогенных трубопроводных систем
— Доставка и монтаж оборудования,включая строительные работы
— Инертизация и опрессовка азотом промышленногооборудования
ИНЕРТИЗАЦИЯ ОБОРУДОВАНИЯ ГАЗООБРАЗНЫМ АЗОТОМ
Задачи
- Подготовка оборудования к запуску после монтажа или ремонта
- Консервация оборудования, исключение возможности внутренней коррозии
- Проверка герметичности системы любым давлением до 170 атм
Почему азот?
- Азот — инертный газ, без содержания влаги
- Вытесняет кислород и останавливает процессы ржавления и окисления
- Экологически безопасен при вдыхании, в том числе для персонала
Быстро, чисто, безопасно:
- Модульное оборудование позволяет решать любые самые сложные задачи
- Не требует разработки и согласований проекта в гос органах
- Время развертывания оборудования – 1-5 дней
- Наша технология позволяет полностью исключить загрязнение маслом и иными примесями
- Оборудование не загрязняет окружающую среду
Этапы решения задачи:
- предварительная техническая проработка проекта, выбор технологического решения
- доставка и организация участка на площадке Заказчика
- организация поставок жидкого газа в буферные емкости в соответствии с графиком
- непосредственное выполнение работ под контролем Заказчика
- демонтаж и вывоз оборудования
Стандартный
общий срок подготовки к выполнению работ не более 1 месяца.
Мы всегда рады помочь Вам и ответить на любые возникшие вопросы!
+7 (911) 272-70-00
+7 (812) 320-16-31
Отправить запрос
[email protected]
Испытание на утечку азота – как провести испытание под давлением с помощью газообразного азота
30 ноября 2020 г.
Из-за его инертных характеристик во многих промышленных процессах газообразный азот используется на нескольких этапах проверки и производства. Газообразный азот можно безопасно использовать для оценки сантехнических работ, проверки целостности трубопроводных сетей и проверки сосудов на наличие утечек.
Узнайте, как работает проверка на утечку газообразного азота в промышленных условиях.
Что такое проверка на герметичность?
Испытание на герметичность — метод проверки промышленного складского и транспортного оборудования (сосудов, насосно-компрессорных труб и трубопроводов) на наличие дефектов. Испытания на герметичность проводятся для того, чтобы убедиться, что вновь установленные системы могут выдерживать температуры и давления, связанные с нормальной работой. Этот тип испытаний является неотъемлемой частью протоколов безопасности в различных промышленных условиях.
Например, испытание газообразным азотом, проводимое перед вводом трубопровода в эксплуатацию, позволяет операторам нефтегазовой отрасли безопасно подготовить свои системы к первому использованию.
Испытания азотом под давлением – Почему именно азот?
Хотя многие промышленные компоненты требуют испытаний под давлением перед установкой, не все методы испытаний подходят для всех компонентов. Например, гидростатические испытания используют воду для проведения испытаний под давлением жидкости, что невозможно в системах, чувствительных к влаге. Коррозионное повреждение испытуемых компонентов из-за протекания через них воды значительно сократит срок их службы. Хотя пневматические испытания представляют собой альтернативу гидростатическим испытаниям, они также могут подвергать испытательные материалы воздействию вредной влаги.
Использование процедуры испытания под давлением азота позволяет операторам обойти проблемы, связанные с другими формами испытаний. Газообразный азот обладает уникальными физическими и химическими свойствами, которые делают его практически инертным. Это делает его идеальным для проверки герметичности.
Из-за своей низкой реакционной способности газообразный азот будет вытеснять кислород и влагу из внутренней среды испытуемых компонентов, одновременно оценивая возможные утечки.
Как проводить испытания под давлением азота
Процедура испытания на утечку азота довольно проста и выполняется в упорядоченной последовательности, чтобы гарантировать максимальную безопасность во время всех аспектов испытания. Хотя конкретные шаги будут различаться в зависимости от характера тестируемого компонента, некоторые общие рекомендации применимы повсеместно.
Перед началом проверки течеискателя газообразного азота тестируемый компонент должен быть изолирован от остальной системы. Этого можно добиться, закрыв соединительные клапаны давления и другие соединительные порты, соединяющие испытательный сосуд/трубопровод с другим системным оборудованием.
После того, как тестовая зона изолирована, газообразный азот, подаваемый из баллона с азотом или синтезируемый местным генератором, направляется в компонент через впускной клапан, оставленный открытым. Загрязнения внутри испытательного сосуда удаляются под низким давлением. Этот тип продувки азотом обычно не превышает 25% номинального давления компонента во время обычной эксплуатации. Эта фаза опрессовки газообразным азотом поддерживается в течение разумного периода времени, чтобы убедиться, что испытуемый компонент выдержит ее без утечек.
После успешного испытания низким давлением прикладываемое давление постепенно, но постоянно увеличивается, чтобы увидеть, насколько хорошо испытуемый компонент может сохранять свою целостность. Хотя испытания будут продолжаться до тех пор, пока не будет достигнуто стандартное номинальное давление испытательного сосуда, верхний предел испытаний будет определяться различными промышленными нормами, касающимися испытаний на герметичность.
Визуальный осмотр на наличие утечек азота осуществляется путем нанесения мыльного раствора на поверхность проверяемого компонента. Утечки, присутствующие в материале, вызывают образование пузырьков газа в дефектных местах, что является ориентиром для ремонта после испытаний. Имейте в виду, что доступны и другие методы обнаружения утечек азота.
Использование контейнеров под давлением вместо генераторов азота на объекте
Газообразный азот, необходимый для проверки герметичности, может быть получен либо из баллонов со сжатым газом, либо с генератора азота на объекте. Хотя использование баллонов с газообразным азотом кажется более дешевым вариантом, в долгосрочной перспективе это значительно дороже по сравнению с единовременным платежом за генератор азота.
После установки PSA или мембранного генератора азота потребуется лишь несколько плановых проверок в год, в то время как покупка газовых баллонов останется постоянной частью оперативного бюджета.
Другие преимущества использования генератора азота на объекте для проверки герметичности включают:
- Синтез газа по запросу в достаточных количествах в любой момент времени
- Сохранение важной промышленной площади (особенно при использовании мобильных генераторов азота), что создает Серьезная проблема с использованием баллонов с азотом
- Эффективное использование газа с минимальными отходами
- Повышение безопасности азота для персонала, поскольку исключается риск, связанный с хранением больших количеств азота
Методы обнаружения утечки газообразного азота
Существует несколько способов обнаружения утечки газообразного азота в промышленных условиях, однако точность зависит от метода. Два наиболее распространенных метода испытаний описаны ниже:
- Коммерческие детекторы азота, используемые для проверки предполагаемых мест утечки в новом оборудовании/компонентах утечки азота
Компания GENERON располагает генераторами азота, необходимыми для эффективного обнаружения утечек.
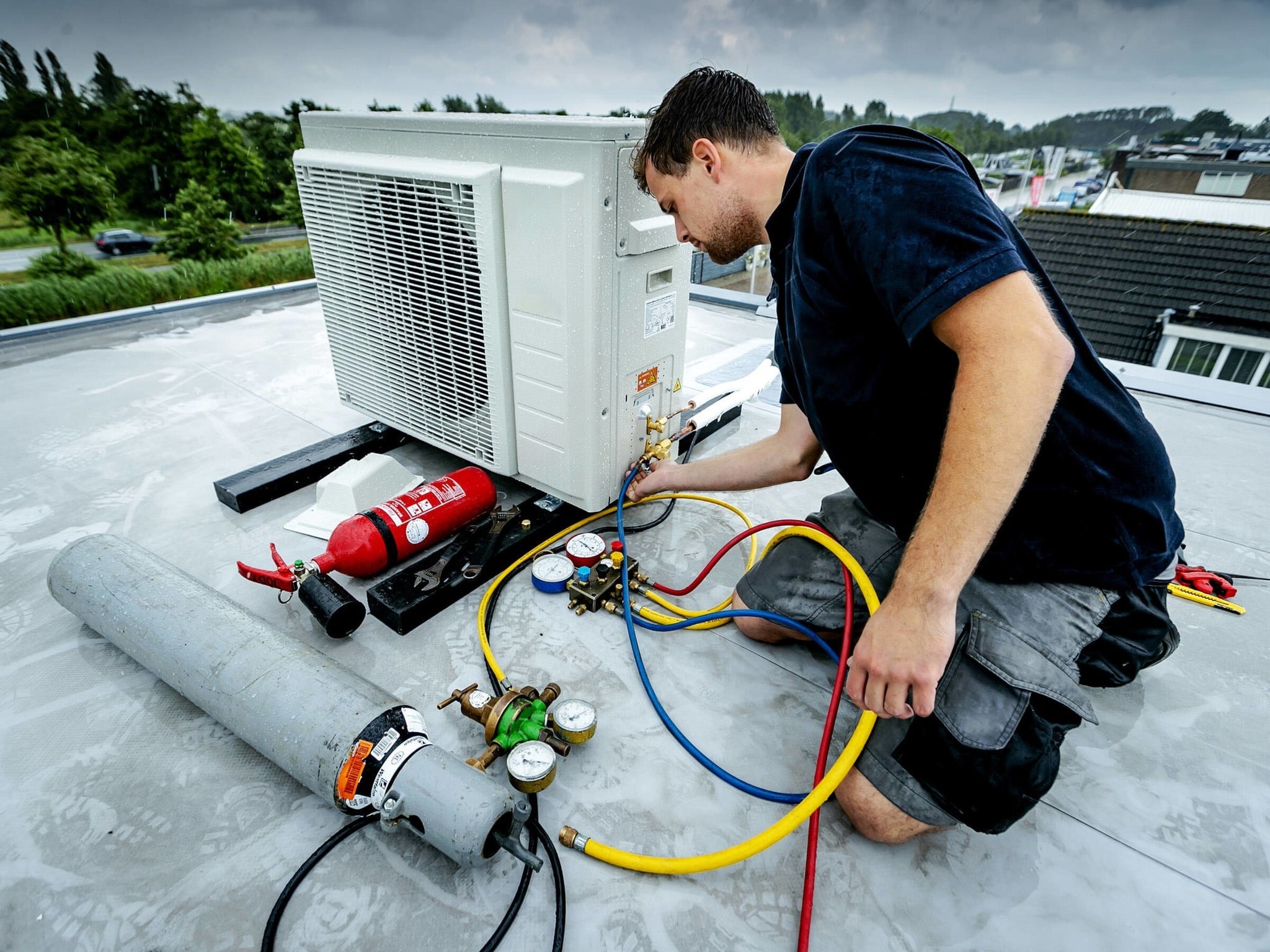
В компании GENERON мы предлагаем передовые решения для производства азота для всех наших клиентов. Наши услуги призваны помочь нашим партнерам максимизировать промышленную производительность, сохраняя при этом рентабельность. Наши генераторы азота обеспечат газ высокой чистоты, необходимый для проведения испытаний по обнаружению утечек.
Свяжитесь с нами сегодня для получения дополнительной информации об услугах и оборудовании для производства азота, которые мы предлагаем.
Процедура испытания на утечку азота – что вам нужно знать
Использование азота для проверки на утечку широко распространено в различных отраслях промышленности. В ряде отраслей промышленности азот используется для проверки утечек, хотя он хорошо известен в нефтяной промышленности для проверки трубопроводов и защитных емкостей.
Когда дело доходит до обнаружения утечек, азот предлагает несколько преимуществ. Благодаря своим инертным свойствам, отсутствию запаха и низкому содержанию влаги азот можно использовать для проведения испытаний под давлением без проблем, связанных с воздухом или водой.
Кроме того, генераторы азота позволяют проводить испытания в любом месте благодаря портативным генераторам азота. В результате азот доступен во всем мире экономичным и удобным способом.
Проверка герметичности: что это такое?
Чтобы убедиться, что каналы, по которым течет азот, не повреждены, проводится процедура проверки на утечку азота. Любой канал, по которому транспортируются промышленные продукты, подвергается этому аналитическому процессу. Во время обычной эксплуатации обнаружение утечек азота может выполняться либо перед первым использованием оборудования, либо через регулярные промежутки времени в течение всей эксплуатации.
Операторам промышленного оборудования необходимо проводить испытания на утечку, чтобы безопасно транспортировать продукт. Это сведет к минимуму риск воздействия на персонал опасных химических веществ, поскольку они перемещаются на протяжении всего производственного процесса. Среди проведенных испытаний — обнаружение утечек в трубопроводах и холодильных системах, проверка уплотнений на предприятиях пищевой промышленности и проверка работоспособности вновь установленных систем пожаротушения.
Испытание азотом под давлением
Чтобы определить готовность трубопровода к полному использованию, опрессовка является важным аспектом его испытания перед первым использованием. При опрессовке анализируются несколько параметров, в том числе:
- Допустимые пропускные способности трубопроводов
- Выявление утечек
- Стабильность соединительной арматуры
- Измерение давления
- Целостность компонентов
Операторы могут оценить, готов ли их трубопровод к работе на полную мощность, рассмотрев параметры. Для проверки трубопровода может потребоваться проведение нескольких испытаний под давлением для выявления и устранения любых проблем.
Испытания азота в медицинских приложениях
Испытания на утечку азота являются важной процедурой для обеспечения герметичности системы в медицинских приложениях, таких как внутривенные (IV) дозаторы жидкости. Это важно для медицинских устройств, поскольку позволяет проверить и проверить целостность устройства. Для начала необходимо настроить электронный регулятор давления, чтобы обеспечить контролируемое давление на внутривенное устройство за счет подачи в него азота. Это можно сделать с помощью различных источников, включая резервуары с жидким азотом, баллоны со сжатым газом или ручные насосы высокого давления.
После того, как электронный регулятор давления отрегулирован, необходимо создать вакуум на устройстве для внутривенных вливаний, чтобы определить наличие утечек. Затем следует медленно выпускать азот через контроллер в устройство для внутривенных вливаний, чтобы измерить любые имеющиеся утечки. Для обеспечения точных результатов важно, чтобы давление и расход азота оставались постоянными на протяжении всего процесса.
Испытание на утечку азота может гарантировать, что медицинское устройство для внутривенных вливаний имеет эффективную герметизацию и, следовательно, в нем нет повреждений. Эта процедура обеспечивает правильную и безопасную работу медицинских устройств при использовании медицинскими работниками на пациентах, что в конечном итоге помогает защитить здоровье и безопасность пациентов, а также целостность продукта в дозаторе для внутривенных вливаний.