что это, его виды и практическое применение, получаемые продукты, перспективы развития метода
Что такое пиролиз – химическая реакция термического разложения исходного вещества. При этом полученная энергия температурного воздействия разрывает внутримолекулярные связи и эта же энергия позволяет получать новые соединения. Реакция идёт без второго реагента и поэтому её можно назвать реакцией термического разложения.
Виды и практическое применение пиролиза
В зависимости от процесса разложения пиролиз может идти при различных температурах. При этом полученные в конце процесса вещества будут отличаться по своему химическому составу. Различается:
- термическое разложение при низкой температуре;
- высокотемпературный пиролиз.
Пиролиз с температурой до 900 градусов считается низкотемпературным и при его проведении получают преимущественно вещества в твёрдом состоянии с небольшой массовой долей газов. При возгонке на высоких температурах, конечным продуктом в основном станут газы. С точки зрения протекания процесса, чем больше получено энергии, тем большей свободой связи обладают молекулы. А чем больше свободы, тем вещество легче, так как расстояния между молекулами увеличиваются.
Перерабатываемые продукты
Использование пиролиза широко. Так, получение продуктов нефтехимии возможно только с применением данного метода. Используемый в металлургии кокс является продуктом пиролиза. Разработаны полигоны бытовых отходов, где их уничтожение происходит с помощью термического разложения. Метод хорош тем, что является безотходным, это в условиях загрязнённой атмосферы Земли актуально.
Получение продуктов нефтехимии
Когда органические сложные соединения разлагаются под воздействием температуры, то происходит получение простых углеводородов. При таком процессе получают этилен и пропилен, а из них разнообразные производные. На их основе получают впоследствии различные ВМС методом полимеризации и синтеза. Крекинг в нефтехимии идёт при 800–900 градусах.
Древесный крекинг
Издавна известна профессия углежогов, которые сжигали древесину без доступа воздуха под землёй и получали древесный уголь. При температуре в 5000 происходит сухая возгонка, при которой получаются ценные продукты – ацетон, смола, уксусная кислота и метанол. При этом углерод остаётся в твёрдом состоянии и называется древесным углём. Такой продукт в дальнейшем используется как высококалорийное топливо или активатор химических процессов.
Начинается пиролиз при температуре в 200 градусов с выделения оксидов углерода. Необходимо отметить и то, что если продукты разложения в дальнейшем сжигать в атмосфере воздуха, то суммарная калорийность их сгорания будет гораздо выше, чем энергия, потраченная на пиролиз.
Химия древесины – наука, которая развивалась первоначально только в России и первые опыты крекинга принадлежат русским учёным.
Уничтожение бытового мусора
Использование пиролиза для уничтожения бытовых отходов и получения за счёт этого энергии перспективно. Главным препятствием является содержание в отходах ядовитых летучих составляющих – хлора, фосфора и серы. Это активные элементы, которые могут связываться с другими продуктами пиролиза и создавать опасные соединения. Переработка шин и полимерных материалов позволяет получить вторичные продукты и экономически оправдана.
Во время пиролиза в аппарате продукт переработки проходит следующие стадии:
- процесс сушки;
- крекинг;
- дожёг остатка в атмосфере;
- очистка газа в поглотителях.
При этом мусоросжигательный завод имеет разные режимы и установки, рассчитанные на тот или иной процесс.
Для полной переработки отходов газовые продукты направляются в специальные поглотительные установки, где происходит их очистка от токсинов.
При этом на мусороперерабатывающем предприятии можно получить:
- тепловую энергию;
- электрическую энергию;
- продукты переработки шин и полимеров.
Экономичным станет производство по утилизации при сортировке мусора. Пока же на полигоны вывозится всё, попадают даже ртутные отходы.
Перспективы в развитии пиролиза
При использовании катализаторов процесс крекинга резко увеличивается и выход продуктов повышается. При этом затруднение вызывает возникающий процесс коксования самих катализаторов. Научные разработки в этом направлении ведутся.
Использование активаторов процесса или ингибиторов, тормозящих вторичные реакции тоже находится в стадии экспериментальных установок. Но и этот способ оптимизации процесса затрудняется в связи с загрязнением выходящего продукта. В настоящее время
В быту распространение получают обогревательные печи на основе крекинга, состоящие из двух камер, в первой из которых происходит возгонка крекингом, а во второй собственно горение.
Сравнение типов очистки духового шкафа
Современная бытовая техника обладают опциями, которые избавляют от многих кухонных хлопот. Одна из таких — автоматическая очистка духового шкафа. Функция освобождает от необходимости залезать в камеру и отскребать застывший на стенках жир. Автоматическая очистка не только спасает от трудоемкого и неприятного процесса, но и помогает правильно обслуживать устройство. Благодаря ей техника служит долго.
Режимы бывают разными. Мы расскажем о трех автоматических способах чистки и сравним их между собой.
Три решения
После приготовления пищи к стенкам и дну духовки пристает жир, который при долгой эксплуатации без уборки превращается в толстую корку. Если заняться устранением такой корки, понадобятся моющие средства, время и терпение. Семь потов сойдет, пока получится добиться чистоты.
Во многих современных устройствах это проблема решается с помощью функции автоматической очистки духовки. Существует три решения: пиролиз, катализ и гидролиз. У каждого из них есть преимущества и недостатки.
Катализ: уборка во время приготовления
Лучший способ держать что-то в чистоте — не допускать загрязнений. Следовать этому неписанному закону помогают установленные внутри духовки каталитические панели. Шершавое мелкопористое покрытие на панелях способствует быстрому окислению жира и ускоряет распад на составляющие: воду и углерод.
Чистка духовки происходит при нагревании от 150°С и выше, то есть процесс будет протекать каждый раз, когда вы готовите при указанной температуре. Специальный режим включать не нужно, что позволяет сэкономить на электричестве.
В каталитических духовках Hansa используются двухсторонние пластины. Такое решение позволяет продлить срок эксплуатации панелей в два раза.
Пиролиз: нагрев до 500°С
Пиролиз — это процесс, при котором происходит термическое разложение остатков еды. Это агрессивная и эффективная процедура, которая занимает около двух часов. Среда нагревается до 500°С, а частички пищи превращаются в пепел. Для безопасности хозяев во время обработки дверь блокируется.
Выдержать высокую температуру помогают нанесенная на внутренние стенки пиролитическая эмаль. Такие модели — самые дорогие на рынке.
Вся внутренняя поверхность очищается, в том числе и дверца шкафа. От вас потребуется лишь пройтись влажной тряпочкой после пиролиза. Во время процедуры противень можно оставить внутри. Духовки с программой «Пиролитическая очистка» также оснащаются системой охлаждения — включенный после процедуры вентилятор выводит с камеры пары и неприятные запахи.
Пиролиз потребляет много электроэнергии. Для духовки с таким режимом уничтожения жира потребуется силовой кабель, выдерживающий высокую мощность.
Гидролиз: обработка паром
Паровой (или гидролизный) режим позволяет быстро и эффективно удалить жир и другие загрязнения. Работает это следующим образом: на противень наливается пол-литра воды, выставляется температура от 90 до 100°С. В течение 30 минут остатки еды размягчаются под воздействием горячего пара.
В некоторых моделях духовых шкафов предусмотрена программа гидролизной очисткой. Кнопку для включения функции можно найти на панели управления. Производители отмечают ее по-разному, поэтому стоит заглянуть в инструкцию и найти нужный значок. Если в вашей духовке отсутствует программа гидролиза, процедуру можно провести самостоятельно, установив рекомендованную температуру и включив нагрев снизу.
После окончания очистки загрязнения можно без труда удалить с помощью мягкой ткани и без применения специальных средств. Однако очистка паром не помогает при уборке давно застывшего слоя жира.
Такие системы еще называют Aqualytic. Ими оборудованы многие модели на отечественном рынке. Гидролизный способ более экономный в сравнении с другими режимами: потребление электроэнергии и цена духовых шкафов не так высоки, как в случае с пиролизом или катализом.
Плюсы и минусы
Если вы не хотите отчищать вручную дверцу, покупайте духовку с пиролизом — это самый действенный метод избавления от жира. Однако и самый дорогой. Менее затратным будет катализ. Такая система не нуждается в надзоре пользователя, зато требует дополнительного ухода: отмывать дверку и дно духового шкафа придется самостоятельно.
Паровой режим — самый недорогой. Он работает при относительно низкой температуре. Добиться хорошего результата в этом случае получится, если использовать метод сразу после приготовления. Главное, не дать жиру засохнуть, тогда пары размягчат загрязнения, и вы без труда уберете их тряпочкой.
| Пиролиз | Катализ | Обработка паром |
Уровень затрат на покупку и энергопотребление | Высокий | Средний | Низкий |
Нужно ли включать функцию отдельно | + | — | + |
Нужно ли убирать вручную после работы системы | + | + | + |
Как часто надо использовать | Не реже, чем через каждые 2 раза после приготовления мяса | Работает постоянно при температуре от 150С | После готовки |
Повышается ли температура в комнате | + | — | — |
Производители духовых шкафов экспериментируют с разными способами очистки. Так, в каталоге Hansa можно найти все три варианта: пиролитическую и каталитическую очистку, а также систему Aqualytic. Выбор зависит от привычек покупателя.
Пиролитические духовые шкафы 👉 Полезные советы
Пиролитические духовые шкафы Körting – воплощение безупречного стиля и богатого функционала. С их помощью вы сможете приготовить разнообразные вкусные и полезные блюда и сократить время уборки. Функция пиролиза позволяет быстро нагреть внутреннее пространство духовки и противни до высокой температуры, при этом все загрязнения сгорают и превращаются в пепел, который затем можно легко удалить с помощью влажной ткани.
Содержание
Как работает пиролитическая очистка
Пиролиз может помочь удалить пятна жира, нагар, мелкие частицы пищи. Этот способ очистки предполагает быстрое повышение температуры внутри духовки до 500 °C. При нагреве все загрязнения полностью сгорают, превращаясь в пепел. В результате очистка происходит без использования химических средств. После начала программы дверца духового шкафа автоматически блокируется. Это необходимо в целях обеспечения безопасности. Пиролитический способ очистки возможен только в электрических духовках, так как газовая бытовая техника не позволяет достичь такой высокой температуры.
Как использовать функцию
Процедуру очистки рекомендуют проводить раз в месяц. Этого достаточно, чтобы поддерживать в порядке внутреннюю поверхность прибора при стандартной частоте эксплуатации. Порядок использования пиролиза:
- Перед очисткой уберите из духовки все оборудование, в том числе телескопические направляющие.
- В зависимости от степени загрязнения выберите подходящую степень очистки. От этого показателя зависят температура и время работы прибора.
- Для обеспечения безопасности в процессе очистки дверца духовки будет заблокирована, в этот момент вы увидите на дисплее символ «ключ».
- На время очистки не размещайте на ручке духового шкафа полотенца, салфетки и другие предметы.
- После окончания программы дождитесь, пока внутренняя поверхность духовки остынет, и соберите пепел мягкой тканью.
Преимущества духового шкафа с функцией пиролитической очистки
- Эффективность. В отличие от каталитической технологии, система пиролиза позволяет удалить любые виды загрязнений, в том числе от сладкого теста, молочных продуктов.
- Очистка труднодоступных мест. Под воздействием высокой температуры устраняются все загрязнения, поэтому после процедуры вам не придется проводить дополнительную ручную чистку.
- Экологичность. Очистка проводится без применения бытовой химии, поэтому вы можете отказаться от использования дополнительных средств и быть спокойными за здоровье вашей семьи.
- Автоматический режим. Очищение происходит без вашего участия – вы можете заняться более важными и приятными делами, посвятить время себе или близким. После завершения программы духовка отключится автоматически.
Особенности модели OKB 892 PEN
Внешний вид и управление. Духовка имеет ширину 60 см, что позволяет встроить ее в стандартный кухонный шкаф. На передней панели расположены поворотные утапливаемые регуляторы. С их помощью осуществляются управление режимом нагрева и настройка температуры. После нажатия регулятор фиксируется внутри панели и образует гладкую поверхность, что облегчает уборку и придает прибору минималистичный вид. Строгое сочетание черного стекла и элементов из нержавеющей стали помогает вписать духовой шкаф в современный интерьер.
Удобство использования. Электронный дисплей отображает время, оставшееся до окончания цикла приготовления пищи, и текущие настройки отложенного старта. Таймер автоматически отключит духовку, поэтому вам не придется отвлекаться от повседневных дел. Противни расположены на телескопических направляющих, чтобы вам было удобнее проверять готовность блюда. Четыре стекла удерживают тепло внутри камеры и делают использование прибора еще более безопасным.
Функционал. Духовка оснащена 11 режимами нагрева, функцией поддержания тепла, автоматическими программами и грилем. С их помощью вы сможете радовать себя и близких разнообразными блюдами из мяса, птицы, рыбы и лакомиться аппетитными десертами. Определить температуру внутри пищи и проконтролировать степень готовности поможет термощуп. В нужный момент он автоматически отключит нагрев.
Выбрать и купить встраиваемую пиролитическую духовку вы можете в официальном интернет-магазине Körting и на сайтах партнеров.
Пиролиз древесины — описание процесса и применение в котлах
Прежде чем описать процесс пиролиза древесины, стоит дать общее понятие пиролиза как процесса.
Итак, пиролиз – это химическая реакция деструкции вещества, вызываемая воздействием высокой температуры. В естественных условиях она протекает совместно с горением.
Последовательность хода процесса покажем на примере древесины:
- нагрев вещества от внешнего источника тепла;
- при температуре около 300 °С начинается процесс разложения вещества и выделения горючих углеводородов;
- так как доступ кислорода не ограничивается, а тепло подводится в виде открытого пламени, при достижении 500 °С количество газов возрастает и происходит их возгорание;
- реакция горения протекает самостоятельно, без внешнего источника тепла. Сжигаемые углеводороды обеспечивают нужное количество теплоты для дальнейшего термического разложения древесины.
Сфера применения пиролиза древесины
В идеальном варианте пиролиз древесины происходит в закрытом пространстве без поступления кислорода и с постоянным подведением тепла извне. Чтобы не расходовать для этой цели дорогие энергоносители, для поддержания процесса используют часть конечного продукта – смесь горючих газов. В состав смеси входит метан, угарный газ (СО) и водород, из негорючих веществ в ней присутствуют углекислый газ и азот.
Получение газообразного горючего из различных отходов деревообработки – это и есть основная сфера применения пиролиза древесины в промышленности.
Пример установки пиролиза древесины
Основное оборудование для технологического процесса — это пиролизные печи (газогенераторы), блоки охладителей и фильтров. Сырье в виде опилок, щепы и прочих отходов загружается в печь и там сжигается при минимальной подаче воздуха. Поскольку производительность установки напрямую зависит от температуры, то в промышленности зачастую применяют так называемый быстрый пиролиз, когда сырье разогревается с высокой скоростью. Смесь газов проходит охлаждение и фильтрацию, после чего закачивается в резервуары для дальнейшей обработки.
Применение пиролиза в котлах
Пиролизные котлы — это группа твердотопливных агрегатов. Она отличается от традиционных котлов прямого горения наличием двух камер вместо одной. По задумке, в первичной камере сжигания идет процесс газификации твердого топлива при подаче недостаточного количества кислорода, а во второй – дожигание выделяющихся пиролизных газов при добавлении вторичного воздуха. Но так ли процесс сжигания проходит на самом деле? Чтобы это понять, надо рассмотреть конструкцию теплогенератора.
На данный момент существует 2 вида пиролизных котлов, разберем устройство каждого подробнее. Самая популярная конструкция – когда первичная топка находится над вторичной. Между ними имеется форсунка прямоугольного сечения, сделанная из огнеупорного кирпича. А теперь внимание: воздух в главную топку нагнетается с помощью вентилятора, частично попадая и в нижнюю камеру для дожигания газов. То есть, принцип пиролиза нарушен изначально, так как вместо ограничения по кислороду вентилятор создает его избыток.
Что это дает? Полное и эффективное сжигание дров, так что и золы не остается. Но этому есть объяснение: сухое дерево не оставляет после себя золы, а только легкий пепел, половина которого просто выдувается вентилятором через форсунку в дымоход. По всем признакам данной конструкции можно присвоить название «котел верхнего дутья», поскольку вентилятор нагнетает воздух в верхнюю камеру. За счет этого возрастает температура горения, увеличивается выход газа, но он тут же сгорает, проходя через форсунку. Подобный алгоритм работы имеет мало общего с химической реакцией пиролиза.
Котлы с естественной подачей воздуха
В другом типе теплогенераторов камеры расположены наоборот: главная топка снизу, вторичная – над ней. Форсунки нет, вместо нее устроен обычный газоход, соединяющий камеры между собой. Вентилятора здесь нет, воздух в обе топки подается естественным путем – за счет тяги дымохода. Причем подача осуществляется по раздельным каналам. Следует отметить, что в данном случае процесс пиролиза древесины организован лучше, горение в топливнике происходит с малым расходом воздуха, его поступление ограничено заслонкой.
О наших котлах
Наши котлы относятся к второму типу — работают на естественной тяге, с сжиганием топлива через окисление отходящих газов при помощи инжекторов в камере сгорания.
Что такое пиролиз (пиролизное горение)
Такое твердое топливо, как древесина и ее производные, при отоплении помещений используется испокон веков. Однако, современные технологии чуть-чуть изменили процесс горения дров, и случилась самая настоящая революция в твердотопливных отопительных системах. На смену обычным котлам на дровах, отличающимся средним коэффициентом полезного действия, пришли пиролизные котлы, названные так в силу того, что них происходит не классическое сжигание древесины, а ее сухая перегонка или пиролизное горение. Для протекания пиролизного горения требуется недостаток кислорода и высокая температура, только тогда твердое топливо начнет разлагаться на летучий газ и твердый остаток с выделением еще большей тепловой энергии.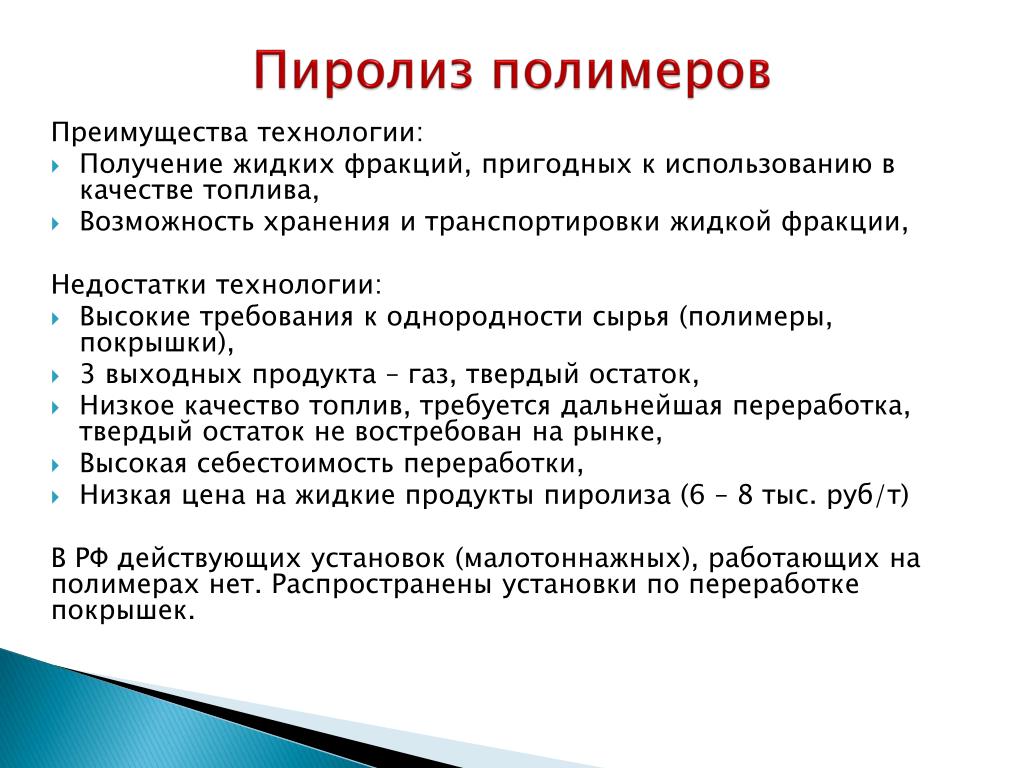
Пиролиз происходит в несколько этапов. Сначала в котле в его приемной камере досушивается древесина и при температуре в 450 С начинается выделение древесного газа. Далее происходит смешивание данного газа с вторичным воздухом, поток которого создает специальный вентилятор в котле. Данная смесь газов начинает гореть при температуре в 560 С. Протекающая экзотермическая реакция в итоге создает максимальные показатели температурного процесса, и при 1100 С происходит дожигание древесного газа. Продолжительность пиролиза существенно возрастает, а значит, повышается КПД отопительного агрегата. Для того, чтобы в котле протекал оптимальный режим пиролизного горения, в его конструкции предусмотрены шиберы. Первоначально пиролизный котел некоторое время работает в обычном режиме сжигания топлива, а при достижении требуемых температур производят полную загрузку дров, и при помощи шибер устанавливается эффективный режим пиролизного горения. Стоит отметить, что пиролизное горение хорошо поддается управлению. Это дало возможность автоматизировать твердотопливные пиролизные котлы. Именно пиролизное горение позволило выявить все скрытые резервы древесного топлива, и существенно увеличить КПД твердотопливных котлов, снизить затраты, а также минимизировать обслуживание отопительной системы человеком.
Еще по теме:
Котлы большой мощности пиролизные Атом
Отопление больших помещений пиролизными котлами
Lummus поставит 14 печей пиролиза для Балтийского Химического Комплекса
2 ноября 2020 года
Компания Lummus Technology поставит 14 печей пиролиза для газохимического комплекса в составе Комплекса по переработке этансодержащего газа (ГХК КПЭГ), создаваемого в районе п. Усть-Луга Ленинградской области.
Контракт на проектирование и поставку печей SRT VI заключен в рамках ЕРС-контракта c China National Chemical Engineering & Construction Corporation Seven, Ltd. (CC7) — EPC-подрядчиком проекта ГХК КПЭГ. Оборудование б<удет поставлено по условиям лицензионного соглашения на технологию производства этилена суммарным объемом (1-я и 2-я очереди) до 3 млн тонн в год, которое оператор проекта ГХК КПЭГ — ООО «Балтийский Химический Комплекс» (дочерняя компания АО «РусГазДобыча») — заключил с Lummus Technology в 2019 году.
Печь пиролиза — основной промышленный реактор этиленовой установки (установки пиролиза). Здесь происходит термическое разложение углеводородов (этана/пропана) с выделением пиролизного газа. Далее газ поступает в секцию извлечения олефинов, где получают этилен полимерного качества, из которого впоследствии производят полиэтилен.
«Проект газохимического комплекса реализуется с применением самых современных, высокоэффективных и экологически безопасных технологических решений. В настоящее время проводится закупка оборудования длительного цикла изготовления. Компактный и надежный модуль Lummus Technology позволяет значительно снизить объем побочных продуктов и сократить удельный расход энергоресурсов. Данный модуль также характеризуется гибкостью в отношении сырья — при нехватке этана допускается подача до 10% пропана», — отметил генеральный директор ООО «Балтийский Химический Комплекс» Константин Махов.
«Это второй крупный контракт на наши SRT-печи пиролиза мирового класса, которые обеспечивают высокую производительность, длительность эксплуатации и энергоэффективность. Это также продолжение нашей работы на Балтийском Химическом Комплексе и преумножение нашего опыта в России, которая является одним из ключевых рынков и где мы признаны одним из лидирующих лицензиаров данной технологии», — сказал президент, главный исполнительный директор Lummus Technology Леон де Брюн.
«Это первый опыт прямого сотрудничества между СС7 и Lummus Technology в сфере производства этилена как в России, так и на мировом рынке. Вслед за подписанным в ноябре 2019 года договором на разработку пакета технологической документации на проектирование установки крекинга этана на Балтийском Химическом Комплексе теперь подписан договор на проектирование и поставку оборудования. Сотрудничество между двумя компаниями продвигается вперед, и опыт взаимодействия в рамках данного проекта будет надежной основой для будущего стратегического партнерства на мировом рынке», — отметил вице-президент СС7 Лун Хайан.
Справка
ООО «Балтийский Химический Комплекс» — оператор проекта строительства газохимического комплекса (ГХК) для производства порядка 3 млн тонн полиэтилена в год. ГХК вместе с интегрированным комплексом по переработке и сжижению природного газа, а также морскими терминалами для отгрузки готовой продукции составляют Комплекс по переработке этансодержащего газа (КПЭГ) — совместный проект, реализуемый АО «РусГазДобыча» и
ПАО «Газпром». Действующие долгосрочные договоры гарантируют сырьевое обеспечение КПЭГ на срок не менее 20 лет.
Благодаря более чем 110-летнему опыту и ориентированности на инновации, результатом которой стали около 130 разработанных технологий и 3400 патентов, Lummus Technology является мировым лидером в разработке и внедрении технологических процессов. Компания является ведущим лицензиаром технологий в нефтехимии, нефтепереработке, газификации и переработке газа, а также поставщиком катализаторов, патентованного оборудования и сопутствующих услуг клиентам по всему миру.
Генеральным подрядчиком проекта газохимического комплекса в составе Комплекса по переработке этансодержащего газа в районе п. Усть-Луга является China National Chemical Engineering & Construction Corporation Seven, Ltd. (CC-7) — стопроцентное дочернее предприятие China National Chemical Engineering Group Corporation Ltd., крупнейшего китайского EPC-подрядчика в нефтегазохимической отрасли. Компания имеет 10-летний опыт работы в России, включая 6 крупных нефтехимических проектов как уже завершенных, так и реализуемых в настоящее время.
Контакты для СМИ
ООО «БХК»: [email protected]
Lummus Technology: [email protected]
СС7: [email protected]
что это за функция, как ей пользоваться
Самая современная и удобная разработка для духовки – пиролитическая система очистки. Эта функция подразумевает самоочищение духового шкафа от загрязнений. Данная функция присутствует в электрических моделях печей.
Система очистки производится за счет высокой температуры нагревания. Это значит, что в духовочной капсуле есть тен из прочного металла, который нагревает все духовое отделение свыше 460°. В результате все остатки продуктов выгорают и превращаются в пепел. В итоге достаточно убрать остатки мусора из духовой коробки.
В ходе выгорания в духовом шкафу создается неприятный запах гари, но за счет установленной системы фильтрации он не проникает наружу. Фильтр не нуждается в чистике или замене, его срок годности рассчитан на весь период эксплуатации данной техники.
Краткая характеристика пиролитической системы духовки
Духовой шкаф с пиролизом – преимущество более дорогих электрических печей. Изготовляются они из тигельной стали. Дверца печки имеет трехслойное, в некоторых случаях четырехслойное теплоизоляционное стекло.
Краткая характеристика:
- функция пиролиза в духовых шкафах обеспечивает идеальную способность самоочищения, в итоге не придется ничего оттирать, отмывать;
- процесс чистки духовки выполняется отдельной независимой программой;
- во время проведения очищения дверца электрической печи автоматически блокируется и разблокируется по завершении процесса;
- очистка электрической печки производится в течение 90-150 минут.
Как пользоваться функцией пиролиза в духовой печи?
Чтобы правильно воспользоваться функцией пиролитической очистки в духовке, необходимо:
- Перед очисткой из духового шкафа обязательно нужно вынуть все металлические перегородки.
- Включить кнопку самоочищения печи.
- После завершения процесса необходимо обработать изнутри все стенки духовой печки.
Важно! Для того чтобы убрать пыль и сгоревшие остатки, необходимо использовать влажную тряпку. Рекомендуется проводить данную операцию каждые 100 часов работы духовки.
Положительные качества
У пиролитической системы очищения довольно много положительных качеств. В сравнении с каталитической и гидролизной технологиями, эта считается более эффективной.
- Не нужно использовать моющие средства.
- Избавляется от самых тяжелых загрязнений: жир, молочные продукты, подгоревшая еда и прочее.
- Очистка проводится для всей внутренней части духового шкафа. Очищаются все труднодоступные участки камеры печи.
- Не требуется дополнительный расход на материалы: в электрической печи предусмотрены все системы безопасности и вентиляции.
Отрицательные качества
Функция пиролиза в духовой камере имеет целый ряд недостатков. Самый главный из них – высокая стоимость печи. Также духовка с такой опцией не избавляет пользователя от дополнительной уборки, все остатки удаляются вручную.
К большому сожалению, функция пиролиза находится только в электрических печах. Минус этого в том, что данная электроника съедает много электроэнергии. А так как опция пиролиза предполагает нагревание печи до высокой температуры, электричество будет затрачиваться в максимальном темпе.
Все внутренние предметы духовой печи очищаются вручную. Решетки и противни должны выниматься в период очистки. И последний минус: система вентилирования не всегда справляется со своей работой. Посторонние запахи могут появляться как в период самоочищения, так и после открытия духовки.
Меры безопасности
Что сможет навредить системе пиролиза в духовке:
- Нельзя перекрывать отверстия для вентилирования.
- Нельзя застилать стенки духового шкафа фольгой.
- Запрещено противень ставить на дно, это портит эмаль духовки.
- Печку нужно использовать только по назначению.
Современный разнообразный выбор печей позволит подобрать именно ту, которая подойдет для вашей кухни. Духовка с пиролизом упростит жизнь любой хозяйки.
Что такое процесс пиролиза?
Новый способ повысить ценность материалов
Пиролиз — это термохимическая обработка, которая может применяться к любому органическому (на основе углерода) продукту. Это можно делать как с чистыми продуктами, так и со смесями. При такой обработке материал подвергается воздействию высокой температуры, и в отсутствие кислорода проходит химическое и физическое разделение на различные молекулы. Разложение происходит благодаря ограниченной термостабильности химических связей материалов, что позволяет им распадаться под воздействием тепла.
Термическое разложение приводит к образованию новых молекул. Это позволяет получать продукты с другим, часто более превосходным характером, чем исходный остаток. Благодаря этой особенности пиролиз становится все более важным процессом для современной промышленности, поскольку он позволяет повысить ценность обычных материалов и отходов.
Пиролиз часто ассоциируется с термической обработкой. Но в отличие от процессов сгорания и газификации, которые включают полное или частичное окисление материала, пиролиз основан на нагревании в отсутствие воздуха.Это делает его преимущественно эндотермическим процессом, обеспечивающим высокую энергоемкость получаемых продуктов.
Продукты пиролиза всегда производят твердые (древесный уголь, биоуголь), жидкие и неконденсируемые газы (h3, Ch5, CnHm, CO, CO2 и N). Поскольку жидкая фаза извлекается из пиролизного газа только во время его охлаждения, в некоторых применениях эти два потока могут использоваться вместе при подаче горячего синтез-газа непосредственно в горелку или камеру окисления (см. «Указания по использованию горячего синтез-газа»).
Во время пиролиза частица материала нагревается от окружающей среды до определенной температуры (заданная температура оборудования Biogreen®). Материал остается внутри пиролизного агрегата и транспортируется шнековым конвейером с определенной скоростью до завершения процесса. Выбранная температура пиролиза определяет состав и выход продуктов (пиролизное масло, синтез-газ и уголь).
Что влияет на результаты процесса пиролиза?
Комментарии закрыты.
Пиролиз — обзор | ScienceDirect Topics
Пиролиз
Пиролиз обычно определяется как термохимическое разложение сырья биомассы при средних (300–800 ° C) и высоких температурах (800–1300 ° C) в инертной атмосфере [15]. Некоторые аналогичные определения приведены в других публикациях [5,8,9,14,16–18].
Общая реакция сырья биомассы составляет
(14.3) Биотопливо + тепло → жидкость + синтез-газ + твердое вещество
Жидкие, синтетические и твердые продукты являются действительно ценными видами топлива и определяются как бионефть, биосингаз и биочаг. соответственно.
Химические реакции в процессе пиролиза включают [19]
(14,4) C + 2h3O → 2h3 + CO2ΔH = + 75 кДж / моль
(14,5) C + h3O → h3 + COΔH = + 131 кДж / моль
( 14.6) Ch5 + 2h3O → 4h3 + CO2 ΔH = + 165 кДж / моль
(14,7) Ch5 + h3O → CO + 3h3ΔH = + 206 кДж / моль
По сравнению с другими термохимическими технологиями, включая сжижение и сжигание, пиролиз обычно имеет следующее Преимущества: (1) основным продуктом является бионефть, и выход может достигать 75%; (2) бионефть может иметь высокое содержание углерода; (3) бионефть может иметь низкое содержание азота и серы; (4) ВТС бионефти может быть очень высокой, например. г. 42 МДж / кг, что сопоставимо с таковыми для ископаемого топлива; (5) время пребывания обычно короткое, что снижает эксплуатационные расходы; (6) желаемый продукт (бионефть, биосингаз или биоуголь) может быть произведен путем корректировки рабочих параметров; (7) бионефть можно легко хранить или транспортировать; и (8) сырье биомассы может не нуждаться в переработке [20].
В соответствии с рабочими параметрами, такими как скорость нагрева, температура пиролиза и время пребывания, обычный электрический пиролиз обычно можно разделить на три группы: (1) медленный пиролиз, (2) быстрый пиролиз и (3) мгновенный пиролиз.В некоторые публикации также включены каталитический пиролиз, микроволновый пиролиз, вакуумный пиролиз и гидропиролиз [2,8,20]. Для медленного пиролиза скорость нагрева, температура пиролиза и время пребывания составляют <1 ° C / с, 300–700 ° C и> 450 с, соответственно. Для быстрого пиролиза они составляют 10–300 ° C / с, 550–1250 ° C и 0,5–20 с соответственно. Для мгновенного пиролиза они составляют> 1000 ° C / с, 800–1300 ° C и <0,5 с соответственно [15,21]. Эти разные условия обычно приводят к разным результатам пиролиза.В таблице 14.2 показаны результаты пиролиза, полученные с использованием различных технологий пиролиза. Замечено, что мгновенный пиролиз обычно способствует производству бионефти с последующим быстрым пиролизом и медленным пиролизом.
Таблица 14.2. Результаты пиролиза, полученные с использованием различных технологий пиролиза [58].
Пиролиз | Условия эксплуатации | Результаты |
---|---|---|
Медленный пиролиз | Температура: 300–700 ° C Время пребывания пара: 10–100 мин Скорость нагрева: 0.1–1 ° C / с Размер сырья: 5–50 мм | Бионефть: ∼30 мас.% Биочар: ∼35 мас.% Газы: ∼35 мас.% |
Быстрый пиролиз | Температура: 400–800 ° C Время пребывания пара: 0,5–5 с Скорость нагрева: 10–200 ° C / с Размер сырья: <3 мм | Бионефть: ∼50 мас.% Биочар: ∼20 мас.% Газы: ∼30 мас.% |
Мгновенный пиролиз | Температура: 800–1000 ° C Время пребывания пара: & lt; 0,5 с Скорость нагрева: & gt; 1000 ° C / с Размер исходного материала: & lt; 0.2 мм | Бионефть: ∼75 мас.% Биочар: ∼12 мас.% Газы: ∼13 мас.% |
Разработана и широко используется новая технология пиролиза, пиролиз с помощью микроволнового излучения [22–24] , и он привлек серьезное внимание из-за своих преимуществ по сравнению с обычным электрическим пиролизом, которые показаны в Таблице 14.3. Эти преимущества обусловлены различными механизмами тепломассообмена. При обычном электрическом пиролизе тепло передается от высокотемпературного газа к поверхности топливных частиц посредством механизма конвекции, а затем оно дополнительно передается от внешней поверхности к внутренней активной зоне через механизм теплопроводности.Образуется температурный градиент снаружи внутрь частицы исходного материала, и высвобождаемые летучие вещества диффундируют из внутреннего ядра к внешней поверхности через область более высоких температур. Для пиролиза с помощью микроволн микроволны проникают в частицу исходного материала, и микроволновая энергия преобразуется в тепловую энергию, которая постоянно накапливается внутри частицы биомассы и затем передается наружу. Образуется температурный градиент от внутренней части к внешней части частицы, и выпущенные летучие вещества диффундируют из внутреннего ядра к внешней поверхности через более низкую температурную область [15].
Таблица 14.3. Сравнение пиролиза с использованием микроволн и обычного электрического пиролиза [15,59,60].
Пиролиз с помощью СВЧ | Обычный электрический пиролиз |
---|---|
Преобразование энергии | Передача энергии |
Бесконтактный нагрев | Контактный нагрев |
Горячая точка | Нет горячей точки |
Селективный | Неселективный |
Более низкая тепловая инерция и более быстрый отклик | Более высокая тепловая инерция и более медленный отклик |
Более низкое потребление энергии | Повышенное потребление энергии |
Быстрый нагрев | Медленный нагрев |
Более короткое время реакции | Более длительное время реакции |
Объемный нагрев | Поверхностный нагрев |
Более высокий уровень контроля | Низкий уровень контроля |
Повышенный выход продукта | л выход продукта |
Пиролиз — обзор | Темы ScienceDirect
B.Пиролиз
Пиролиз — это процесс химического разложения органических материалов под действием тепла в отсутствие кислорода. Практически невозможно достичь полностью бескислородной атмосферы, поэтому пиролитические системы работают с меньшими стехиометрическими количествами кислорода. Поскольку некоторое количество кислорода будет присутствовать в любой пиролитической системе, всегда будет небольшое количество окисления. Также десорбция будет происходить, когда в сырье присутствуют летучие или полулетучие соединения.
Во время пиролиза [5] органические соединения превращаются в газообразные компоненты вместе с некоторыми жидкостями, такими как кокс, т.е.е. твердый остаток связанного углерода и золы. Производятся CO, H 2 , CH 4 и другие углеводороды. Если эти газы охлаждают и конденсируются, образуются жидкости, оставляющие маслянистые остатки смолы и воду с высокими концентрациями ТОС. Пиролиз обычно происходит при давлении выше атмосферного при температуре, превышающей 430 ° C. Вторичные газы требуют отдельной обработки, например, с помощью вторичной камеры сгорания, сжигания на факеле и частичной конденсации. Твердые частицы должны удаляться дополнительными средствами контроля загрязнения воздуха, например.грамм. тканевые фильтры или мокрые скрубберы.
Обычные методы термической обработки, такие как вращающаяся печь, печь с вращающимся подом или печь с псевдоожиженным слоем, используются для пиролиза отходов. Обжиговые печи или печи, используемые для пиролиза, могут иметь ту же конструкцию, что и печи, используемые для сжигания (т. Е. Сжигания), обсуждаемые ранее, но работать при более низких температурах и с меньшим количеством воздуха, чем при сжигании.
Целевые группы загрязняющих веществ для пиролиза включают полулетучие органические соединения (SVOC), включая пестициды, ПХД, диоксины и ПАУ.Он позволяет отделять органические загрязнители от различных отходов, в том числе от нефтеперерабатывающих заводов, каменноугольной смолы, консервантов для древесины, загрязненных креозотом и углеводородных почв, смешанных радиоактивных и опасных отходов, обработки синтетического каучука, а также процессов окраски и нанесения покрытий. Системы пиролиза могут использоваться для обработки различных органических загрязнителей, которые химически разлагаются при нагревании (например, «крекинг»). Пиролиз неэффективен ни для разрушения, ни для физического разделения неорганических соединений, которые сосуществуют с органическими веществами в загрязненной среде.Летучие металлы могут быть удалены и преобразованы, но их массовый баланс, конечно, не изменится.
ПИРОЛИЗ БИОМАССЫ | AltEnergyMag
Введение
Пиролиз — это термическое разложение биомассы, происходящее в отсутствие кислорода. Это фундаментальная химическая реакция, которая является предвестником процессов горения и газификации и протекает естественным путем в первые две секунды. Продукты пиролиза биомассы включают биоуголь, бионефть и газы, включая метан, водород, монооксид углерода и диоксид углерода.В зависимости от термической среды и конечной температуры, пиролиз будет давать в основном биоуголь при низких температурах, менее 450 ° C, когда скорость нагрева довольно низкая, и в основном газы при высоких температурах, превышающих 800 ° C, с высокой скоростью нагрева. При промежуточной температуре и относительно высоких скоростях нагрева основным продуктом является бионефть.
Пиролиз можно проводить в относительно небольших масштабах и в удаленных местах, что увеличивает удельную энергию ресурса биомассы и снижает затраты на транспортировку и погрузочно-разгрузочные работы.Теплопередача является критической областью пиролиза, поскольку процесс пиролиза является эндотермическим, и для удовлетворения технологических потребностей в тепле необходимо обеспечить достаточную поверхность теплопередачи. Пиролиз предлагает гибкий и привлекательный способ превращения твердой биомассы в легко хранимую и транспортируемую жидкость, которую можно успешно использовать для производства тепла, энергии и химикатов.
Рисунок 1 Условия процесса пиролиза биомассы
Сырье для пиролиза
В процессах пиролиза можно использовать широкий спектр сырья биомассы.Процесс пиролиза очень зависит от содержания влаги в сырье, которое должно составлять около 10%. При более высоком содержании влаги образуется большое количество воды, а при более низком уровне существует риск того, что в результате процесса будет образовываться только пыль, а не масло. Потоки отходов с высоким содержанием влаги, такие как шлам и отходы мясопереработки, требуют сушки перед пиролизом.
Эффективность и характер процесса пиролиза зависят от размера частиц исходного сырья.Большинство технологий пиролиза позволяют обрабатывать только мелкие частицы размером максимум 2 мм с учетом необходимости быстрой передачи тепла через частицы. Требование малого размера частиц означает, что сырье должно быть уменьшено в размере перед использованием для пиролиза.
Рисунок 2 Взгляд на доступность сырья и энергетические продукты пиролиза биомассы
Виды пиролиза
Пиролиз Процессы можно разделить на медленный пиролиз или быстрый пиролиз.Быстрый пиролиз в настоящее время является наиболее широко используемой системой пиролиза. Медленный пиролиз занимает несколько часов и приводит к получению биоугля в качестве основного продукта. С другой стороны, быстрый пиролиз дает 60% биомасла и требует секунд для полного пиролиза. Кроме того, он дает 20% биоугля и 20% синтез-газа. Процессы быстрого пиролиза включают пиролиз с неподвижным слоем с открытым сердечником, быстрый абляционный пиролиз, циклонный быстрый пиролиз и системы быстрого пиролиза с вращающимся сердечником. Существенными характеристиками процесса быстрого пиролиза являются:
- Очень высокие скорости нагрева и теплопередачи, для которых требуется тонко измельченный материал.
- Тщательно контролируемая температура реакции около 500 ° C в паровой фазе
- Время пребывания паров пиролиза в реакторе менее 1 с
- Гашение (быстрое охлаждение) паров пиролиза с получением продукта бионефти.
Использование биомасла
Бионефть представляет собой жидкость темно-коричневого цвета, по составу аналогичную биомассе. Он имеет гораздо более высокую плотность, чем древесные материалы, что снижает затраты на хранение и транспортировку.Биомасло не подходит для прямого использования в стандартных двигателях внутреннего сгорания. В качестве альтернативы масло можно улучшить либо до специального моторного топлива, либо с помощью процессов газификации до синтез-газа, а затем биодизеля. Бионефть особенно привлекательна для совместного сжигания, поскольку с ней легче обращаться и сжигать, чем твердое топливо, и ее дешевле транспортировать и хранить. Совместное сжигание биомасла было продемонстрировано на газовой электростанции мощностью 350 МВт в Голландии, когда был успешно заменен 1% мощности котла.Именно в таких приложениях биомасло может предложить значительные преимущества перед твердой биомассой и газификацией из-за простоты обращения, хранения и сжигания на существующей электростанции, когда нет необходимости в специальных процедурах запуска. Кроме того, биомасло также является жизненно важным источником широкого спектра органических соединений и специальных химикатов.
Важность Biochar
Растущая озабоченность по поводу изменения климата привлекла внимание к биочару. Сжигание и разложение древесной биомассы и сельскохозяйственных остатков приводит к выбросу большого количества диоксида углерода.Biochar может накапливать этот CO2 в почве, что приводит к сокращению выбросов парниковых газов и повышению плодородия почвы. В дополнение к его способности связывать углерод, biochar имеет несколько других преимуществ.
- Biochar может увеличить количество доступных питательных веществ для роста растений, удержания воды и уменьшить количество удобрений, предотвращая вымывание питательных веществ из почвы.
- Biochar снижает выбросы метана и закиси азота из почвы, тем самым еще больше сокращая выбросы парниковых газов.
- Biochar может использоваться во многих приложениях в качестве замены других энергетических систем, работающих на биомассе.
- Biochar можно использовать в качестве удобрения почвы для увеличения урожайности растений.
Выводы
Пиролиз биомассы привлекает большое внимание из-за его высокой эффективности и хороших экологических характеристик. Это также дает возможность перерабатывать сельскохозяйственные остатки, древесные отходы и твердые бытовые отходы в экологически чистую энергию.Кроме того, связывание биоугля может иметь большое значение для выбросов ископаемого топлива во всем мире и выступать в качестве основного игрока на мировом углеродном рынке с его надежной, чистой и простой технологией производства.
7. Исследование процессов пиролиза биомассы
7. Исследование процессов пиролиза биомассы.7.1. Общее введение
7.2. Система пиролиза биомассы
7.3. Продукты и их характеристики
7.4. Предварительная обработка и определение характеристик исходного сырья
7.5. Установлен пилотный реактор с вращающимся конусом в САУ
7.1.1 Что такое пиролиз?
Пиролиз — это термическая деградация либо при полном отсутствии окислителя, либо с такой ограниченной подачей, что газификация не происходит в значительной степени или может быть описана как частичная газификация.Используются относительно низкие температуры от 500 до 800 ° C по сравнению с 800 до 1000 ° C при газификации. Обычно производятся три продукта: газ, пиролизное масло и древесный уголь, относительные пропорции которых очень сильно зависят от метода пиролиза, характеристик биомассы и параметров реакции. Быстрый или мгновенный пиролиз используется для максимального увеличения количества газообразных или жидких продуктов в зависимости от используемой температуры.
7.1.2 История пиролиза биомассы
Чем интересен пиролиз?
Есть несколько способов использовать энергию, содержащуюся в биомассе, от прямого сжигания до газификации и пиролиза.Выбор наиболее прибыльного метода рекуперации энергии из биомассы определенного типа является и наиболее важным шагом на пути к прибыльным инвестициям.
Прямое сжигание — это старый способ использования биомассы. Биомасса полностью превращается в тепло, но эффективность составляет всего около 10 процентов. Газификация доводит до максимального уровня крекинг биомассы, полностью превращая ее в горючий газ перед сжиганием. Производство древесного угля, медленный пиролиз древесины при температуре 500 ° C — это процесс, который производители древесного угля использовали на протяжении тысячелетий.Древесный уголь — бездымное топливо, которое до сих пор используется для отопления. Его первое технологическое использование можно отнести к железному веку, когда древесный уголь использовался при плавке руды для производства железа. Производство древесного пара обычно связано с копчением, которое является одним из старейших методов консервирования пищевых продуктов, вероятно, применяемым с момента развития кулинарии на огне. Эти пары, содержащие природные консерванты, такие как формальдегид и спирт, использовались в качестве исходного сырья. Основная привлекательность — небольшие и очень простые установки, которые можно изготавливать с очень низкими инвестиционными затратами.Недостаток — довольно низкая выработка энергии и загрязнение воздуха.
Пиролиз биомассы привлекателен, потому что твердая биомасса и отходы очень сложны и дороги в обращении. легко превращается в жидкие продукты. Эти жидкости, такие как сырая бионефть или суспензия древесного угля из воды или масла, имеют преимущества при транспортировке, хранении, сжигании, модернизации и гибкости в производстве и сбыте. Плотность энергии сведена в Таблицу 7.1.
Неочищенное пиролизное масло представляет собой холостой флюид, который часто называют бионефть, пиролизное масло или просто нефть.Другой основной продукт — это суспензия, которую можно приготовить из отходов и древесного угля с добавлением химикатов для стабилизации суспензии. Сообщалось о стабильной и подвижной концентрации до 60% мас. Суспензии также можно приготовить из масла и древесного угля.
На пилотной установке газ обычно сжигается на факеле, но в промышленном процессе он будет использоваться для управления процессом или для сушки топлива или выработки электроэнергии.
При транспортировке важна насыпная плотность, некоторые расчетные значения приведены в таблице 7.1 Смеси нефти и навозной жижи имеют явное преимущество перед древесной щепой и соломой по объемной плотности при транспортировке и заметны по удельной энергии.
Для сбора биомассы на большие расстояния эта разница может быть решающим фактором.
Хранение и транспортировка могут быть важны из-за сезонных колебаний производства, и всегда будет требоваться некоторое хранение. Помимо насыпной плотности и учета энергии, важно, чтобы сырая биомасса ухудшалась во время хранения из-за процесса биологического разложения.Однако уголь очень стабилен и биологически не разлагается. Еще одним важным фактором является обращение с жидкостью, при котором жидкости имеют значительные преимущества перед твердыми веществами.
Обычно жидкие продукты легче контролировать в процессе сгорания, и это важно при модернизации существующего оборудования. Существующие горелки, работающие на жидком топливе, не могут полностью работать на твердой биомассе без какой-либо модификации устройства, что может не быть заинтересовано в неопределенных рынках топлива. Тем не менее, бионефти, суспензии полукокса и воды, вероятно, потребуются лишь относительно небольшая переделка оборудования или даже не потребуется в некоторых случаях.Горелки для угля с электроприводом относительно легко могут принять древесный уголь в качестве частичной замены топлива, если содержание нарушения совместимо с конструкцией горелки.
На электростанциях газовые турбины могут легко работать на биомасле и жидком топливе, хотя при этом требуется щелочная зола в полукоксовом растворе. Некоторые модифицированные двигатели могут использоваться для использования модернизированного масла. В некоторых странах. существует рынок кусков древесного угля и брикетов для отдыха и промышленного использования.
Табл.7.1 Энергетические и плотностные характеристики
Корм | Насыпная плотность кг / м 3 ) | Теплотворная способность в сухом виде (ГДж / т) | Плотность энергии (ГДж / м 3 ) |
солома | 100 | 20 | 2 |
щепа | 400 | 20 | 8 |
пиро-масло | 1200 | 25 | 30 |
уголь | 300 | 30 | 9 |
суспензия угольной воды (50/50) | 1000 | 15 | 15 |
суспензия угольного масла (20/80) | 1150 | 23 | 26 |
7.1.3 Общее введение в процесс пиролиза биомассы
На сегодняшний день существует множество видов процессов пиролиза биомассы, таких как обычные, мгновенные или быстрые, которые зависят от параметров реакции. Однако типичный процесс пиролиза можно описать следующим образом:
Биомассу предварительно измельчают и сушат, чтобы полностью контролировать процесс. Таким образом, биомасса подается в реактор с воздухом, достаточным для сжигания той части биомассы или теплоносителя (песка или другого), обеспечивающего тепло, необходимое для процесса.Система циклонов и конденсаторов позволяет восстанавливать продукты. Вообще говоря, система пиролиза биомассы имеет дело со многими аспектами: посадка биомассы, предварительная обработка, процесс пиролиза, использование и обновление продуктов, стоимость и экономическая оценка. Ниже будут рассмотрены новейшие технологии пиролиза биомассы в странах Европы и США
.7.2.1 Классификация пиролиза
Пиролиз применялся на протяжении веков для производства древесного угля.Это требует относительно медленной реакции при очень низких температурах для максимального увеличения выхода твердого вещества. Совсем недавно исследования механизмов пиролиза предложили способы существенного изменения пропорций газа, жидких и твердых продуктов путем изменения скорости нагрева, температуры и времени пребывания.
Высокая скорость нагрева, до заявленной 1000 ° C / с или даже 10000 ° C / с, при температуре ниже примерно 650 ° C и с быстрым охлаждением, вызывает конденсацию жидких промежуточных продуктов пиролиза до того, как дальнейшая реакция развалится. частицы с более высокой молекулярной массой в газообразные продукты.Высокие скорости реакции также сводят к минимуму образование полукокса, и при некоторых условиях, по-видимому, не образуется никакого полукокса. При высокой максимальной температуре основным продуктом является газ. Пиролиз при таких высоких скоростях нагрева известен как быстрый или мгновенный пиролиз в зависимости от скорости нагревания и времени пребывания, хотя различия нечеткие. В другой работе была предпринята попытка использовать сложные механизмы разложения путем пиролиза в необычной среде. Основные варианты пиролиза перечислены в таблице 7.2, а характеристики основных моделей пиролиза сведены в таблицу 7.3.
Таблица 7.2 Вариант технологии пиролиза
Тех. | Время пребывания | Скорость нагрева | Температура ° C | Продукты |
карбонизация | дней | очень низкий | 400 | уголь |
Обычный | 5-30 мин | низкий | 600 | нефть, газ, уголь |
Быстро | 0.5-5с | очень высокий | 650 | биомасло |
Вспышка | <1 с | высокая | <650 | биомасло |
Вспышка газа | <1 с | высокая | <650 | химикаты, газ |
Ультра | <0.5 | очень высокий | 1000 | химикаты, газ |
Вакуум | 2-30с | средний | 400 | биомасло |
Hydro-pyro. | <10 с | высокая | <500 | биомасло |
Метано-пиро. | <10 с | высокая | > 700 | химических веществ |
Таблица 7.3 Характеристики пиролизных технологий
Низкая температура вспышки | Высокая температура вспышки | Медленный | Карбонизация | ||
Сырье | |||||
Размер канала | малый | малый | умеренный | большой | |
Влажность | v.низкий | v. Низкий | низкий | низкий | |
Параметры | |||||
Температура ° C | 450-600 | 650-900 | 500-600 | 450-600 | |
Давление, бар | 1 | 0.1-1 | 1 | 1 | |
Макс. расход, т / ч | 0,05 | 0,02 | 5 | 10 | |
Товар | |||||
Газ,% мас. Сухой | <30 | <70 | <40 | <40 | |
МДж / Нм3 | 10-20 | 10-20 | 5-10 | 2-4 | |
Жидкость% | <80 | <20 | <30 | <20 | |
МДж / кг | 23 | 23 | 23 | 10-20 | |
Цельный% | <15 | <20 | <30 | <35 | |
МДж / кг | 30 | 30 | 30 | 30 |
7.2.2 Текущее состояние технологий
В Европе демонстрационная установка производительностью 500 кг / ч в настоящее время работает в Италии для производства жидкости. Планируется, что на основе этой технологии появятся небольшие коммерческие предприятия в Италии, Испании и Греции в качестве проектов LEBEN. Пилотная установка производительностью 250 кг / ч, основанная на процессах Ватерлоо, была построена в Испании. Несколько заводов работают на демонстрационном уровне для отстоя сточных вод и бытовых отходов в Западной Германии с производительностью до 2 т / ч на основе медленного пиролиза.
В другом месте в Северной Америке работает ряд демонстрационных установок для мгновенного пиролиза с производительностью до 25 кг / ч с планами нескольких коммерческих разработок с производительностью до 40 кг / ч, включая коммерческую установку, запланированную в Калифорнии на основе абляционный пиролиз и пиролиз осадка сточных вод SERI в Канаде и Австралии. Примеры текущих исследований и разработок перечислены в Таблице 7.4. Некоторые свойства, о которых было сообщено, суммированы и сравниваются в Таблице 7.5.
A. Реактор с неподвижным слоем
Древесный уголь можно производить с помощью реактора с неподвижным слоем, в котором сырье биомассы частично газифицируется воздухом. Компания Bio-Alternative SA использовала газогенератор с нисходящим потоком с неподвижным слоем газа диаметром 1 м и высотой 3 м (Bridgwater and Bridgw, 1991). с производительностью по биомассе 2000 кг / ч. Продуктами этого процесса являются газ, вязкие смолы и древесный уголь, выход которых максимален. Для древесины пихты и бука был достигнут выход древесного угля 300% по весу в пересчете на загружаемую древесину.Все продукты используются в качестве энергоносителей.
Таблица 7.5. Характеристики различных технологий пиролиза бионефти
Технологии | ГИТ | Энсин | лавал | СЕРИЯ | Твенте | |
Температура [° C] | 500 | 550 | 480 | 510 | 600 | |
Давление [бар абс.] | 1.0 | 1,0 | 0,01 | 1,0 | 1,0 | |
Расход [кг / ч] | 50 | 50 | 30 | 30 | 12 | |
dp [мм] | 0,5 | 0.2 | 10 | 5 | 0,5 | |
т газа [с] | 1,0 | 0,4 | 3 | 1 | 0,5 | |
т твердых [с] | 1,0 | 0,4 | 100 | 0.5 | ||
Выход газа [мас.%] | 30 | 25 | 14 | 35 | 20 | |
Выход гудрона [мас.%] | 60 | 65 | 65 | 55 | 70 | |
Выход полукокса [мас.%] | 10 | 10 | 21 | 10 | 10 | |
Характеристики гудрона (на мокрой основе) | ||||||
Плотность | 1.23 | 1,21 | 1,23 | 1,20 | 1,20 | |
Вязкость [cp] | 10 (60c) | 90 (25c) | 5 (40c) | 90 (30c) | 80 (20c) | |
C мас.% | 39.5 | 45,5 | 49,9 | 54,4 | 43,2 | |
H вес.% | 7,5 | 7,0 | 7,0 | 5,7 | 8,2 | |
0 мас.% | 52,6 | 45.4 | 43,0 | 39,8 | 48,6 | |
HHV [МДж / кг] | 24 | 19,3 | 21 | 15 | 25 | |
Вода в гудроне [мас.%] | 29 | 16 | 18 | 15 | 25 | |
Выход продукта | ||||||
% по массе жидкости | 21 | 59 | 66 | 70 | ||
вода | 26 | 26 | 10 | 10 | ||
симв. | 21 | 15 | 14 | 10 | ||
газ | 32 | – | 10 | 10 |
Таблица 7.4 Сравнение технологий процесса пиролиза: ранжирование по желаемым продуктам
Технологии | Организация | Производительность (кг / ч) | Требуемый газ / смола / уголь | T (° C) | |
товар | (Вес%) | ||||
Фиксированная кровать | Био-альтернатива | 2000 | Char | 55/15/30 | 500-800 |
псевдоожиженный слой | ТЕБЯ | 500 | Газ | 80/10/10 | 650–1000 |
Радиационная печь | Univ.Сарагоса | 100 | Газ | 90/8/2 | 1000–2000 |
Обычный | Альтен (КТИ + Itaenergy) | 500 | Смола | ||
Циркуляционный псевдоожиженный слой | Энсин Инжиниринг | 30 | Смола | 25/65/10 | 450-800 |
Быстро увлеченный поток | Технологический исследовательский институт Джорджии. | 50 | Смола | 30/60/10 | 400–550 |
Вакуум | Университет Лаваля | 30 | Смола | 15/65/20 | 250-450 |
Вихревой реактор | Исследования солнечной энергии Ins. | 30 | Смола | 35/55/10 | 475-725 |
низкая температура | Тюбингенский университет | 10 | |||
Flash с псевдоожиженным слоем | Университет Ватерлоо | 3 | Смола | 20/70/10 | 425-625 |
Реактор с вращающимся конусом | Univ.Твенте | 10 | Смола | 20/70/10 | 500-700 |
B. Реактор с псевдоожиженным слоем
Хорошо известная технология реакторов с псевдоожиженным слоем применялась Косстрином (1980), Гуртеем и др. (1987) и Скоттом и др. (1988). Выходы смолы, производимые реактором с псевдоожиженным слоем среднего масштаба (100 кг / ч), довольно низкие из-за крекинга паров в больших объемах слоя и надводного борта.Технология реакторов с псевдоожиженным слоем предлагает хорошие возможности для газификации сырья биомассы с минимальным образованием смол. В этом случае материал слоя следует выбирать на основе оптимальных характеристик каталитического крекинга гудрона. Однако, если продуктом является деготь, следует применить некаталитический неглубокий псевдоожиженный слой с последующим немедленным гашением газообразных продуктов.
C. Специфические технологии производства бионефти.
Производство бионефти максимально при средних температурах процесса (450-650) и коротком времени пребывания паров в реакторе.Полезными критериями для выбора технологий пиролиза для производства бионефти являются: i) выход биомасла на единицу массы древесины, который должен быть как можно более высоким, ii) мощность реактора процесса должна быть достаточно большой, чтобы ограничить количество шагов по увеличению мощности до полной мощности завода. Технологии пиролиза, включенные в следующий обзор, выбираются на основе этих критериев. Соответственно, было решено рассматривать только процессы с выходом биомасла более 50 мас.% В пересчете на сухую древесину и производительностью установки более 10 кг / ч.Схематическое расположение четырех известных технологий представлено на рис. 7.1; их особенности приведены в таблице 5 вместе с характеристиками «процесса вращения конуса Твенте».
а. Реактор с увлеченным потоком
Пиролиз биомассы в реакторе с увлеченным потоком был изучен Гортоном и др. (1990) в Технологическом институте Джорджии, Атланта, Джорджия, США. Технологическая схема их процесса представлена на рис. 7.1a. Вертикальная трубка реактора имеет длину 6,4 м и внутренний диаметр 0 мкм.15м. Воздух и пропан вводятся стехиометрически и сгорают в нижней части их реактора. Полученный горячий дымовой газ течет вверх по трубе, проходя через точку сбора биомассы. Таким образом, тепловая энергия горючего газа используется для нагрева частиц биомассы и, при необходимости, для обеспечения тепла реакции пиролиза. Типичные рабочие условия — отношение массового расхода газа-носителя к массовому потоку пиролиза около 4, температура на входе в реактор 900 ° C, атмосферное давление в реакторе и пропускная способность реактора 500 кг.час Недостатком является необходимость в большом количестве газа-носителя (азота).
г. Реактор с циркулирующим псевдоожиженным слоем.
Реактор с восходящим потоком циркулирующей жидкости эксплуатируется компанией Ensyn в Оттаве, Канада (Graham, 1988). Рис. 7.1b показывает, что частицы биомассы и предварительно нагретый песок подаются вместе в нижнюю часть реактора с циркулирующей жидкостью. К сожалению, в литературе нет данных о размерах и расходах предварительно нагретого газа-носителя и песка для этого процесса.Обычно этот реактор работает при температуре 600 ° C и производительности по биомассе 100 кг / ч. Утверждается, что 60% биомасла можно получить из древесины тополя в качестве исходного сырья. Использование песка в качестве теплоносителя дает преимущество компактной конструкции из-за высокой скорости передачи тепла от песка к частицам биомассы. Еще одно преимущество — короткое время пребывания газа, за счет которого подавляется вторичный крекинг гудрона. Когда этот реактор становится масштабным, особое внимание следует уделять быстрому смешиванию частиц биомассы с твердым теплоносителем.И снова потребность в газе-носителе является недостатком.
г. Вакуумная печь-реактор
Вакуумный пиролиз полярной осины в многоподовом реакторе был изучен Роем и др. (1992, 1993) в Университете Лаваля, Квебек, Канада. Шесть обогреваемых подов диаметром 0,7 м установлены наверху общей высотой 2 м как часть реактора, показанного на рис. 7.1c. Древесина подается в верхний отсек реактора и транспортируется вниз под действием силы тяжести и скребков, которые в настоящее время находятся в каждом отсеке.Если биомедицина полностью преобразована, нижнее отделение будет содержать только древесный уголь, который можно легко удалить из реактора. Температура верхнего пода составляет около 200 ° C и увеличивается по направлению к нижней части реактора, где она достигает 400, ° C, , для получения максимального количества бионефти. Вакуумный насос используется для поддержания давления в реакторе на уровне 1 кПа. Трудность увеличения размера реактора связана с установкой вакуумного насоса большой мощности, который чувствителен к загрязнению, а также является очень дорогостоящим.
г. Вихревой реактор
Вихревой реактор был построен Diebold and Power (1988) в Исследовательском институте солнечной энергии, Голден, Ко. США. Диаметр трубы этого реактора составляет 0,13 м, а длина 0,7 м. Для правильной работы реактора частицы биомассы должны быть увлекаются потоком азота со скоростью 400 м / с и входят в трубку реактора по касательной (см. рис. 7.1d). В таких условиях частицы биомассы испытывают высокие центробежные силы, которые вызывают высокие скорости абляции частиц на нагретой стенке реактора (625 ° C).Абляционные частицы оставляют на стенке жидкую пленку биомасла, которая быстро испаряется. Если древесные частицы не преобразованы полностью, они могут быть переработаны с помощью специального контура рециркуляции твердых частиц. В своей статье Диблод и Пауэр (1988) оценивают количество циклов, необходимых для достижения полного преобразования частиц биомассы, примерно в 15, что считается слишком высоким. Однако до сих пор было получено 80 мас.% Биомасла на основе сухой древесины.
В зависимости от используемого процесса первичные продукты могут быть газовыми, жидкими и твердыми.Большинство проектов заинтересованы в жидких продуктах из-за их высокой энергоемкости и потенциала замещения нефти.
Жидкость при образовании приближается к биомассе по элементному составу с немного более высокой теплотворной способностью 20-25 МДж / кг и состоит из очень сложной смеси кислородсодержащих углеводородов. Сложность возникает из-за разложения лигнина и широкого спектра фенольных соединений. Жидкость часто называют маслом, но она больше похожа на деготь. Это также может быть разложено до жидкого углеводородного топлива.Неочищенная жидкость пиролиза представляет собой густую смолистую жидкость с содержанием воды до 20% и вязкостью как тяжелая нефть.
Твердым продуктом процесса пиролиза является уголь, который имеет ограниченное применение в развитых странах для металлургии и отдыха. Альтернативный подход к жидким продуктам заключается в измельчении автомобиля и замачивании его водой со стабилизатором. Сообщалось о стабильной и подвижной концентрации до 60 мас.%. Суспензию также можно приготовить из биомасла и полукокса, но максимальная концентрация твердого вещества составляет 30%.
Газовый продукт пиролиза обычно представляет собой топливный газ MHV около 15-22 МДж / м.миль 3 . или низковольтный топливный газ с концентрацией около 4-8 МДж / Нм 3 от частичной газификации в зависимости от параметров подачи и обработки.
Рис. 7.1 Схема четырех известных технологий. A. Реактор с увлеченным потоком (GIT)
Рис. 7.1 Схематическое расположение четырех известных технологий. B. Реактор с циркулирующим псевдоожиженным слоем (ENSYN)
Фиг.7.1 Схематическое расположение четырех известных технологий. C. Многоподовый реактор (Университет Лаваля)
Рис. 7.1 Схематическое расположение четырех известных технологий. D. Вихревой реактор (SERI)
Сырье, обычно рассматриваемое для термохимической переработки, — это древесина и древесные отходы, энергетические культуры, такие как лесное хозяйство с коротким оборотом и сладкое сорго, сельскохозяйственные отходы и мусор. Основными техническими критериями пригодности для термохимической обработки являются влажность, зольность и характеристики.Основными экономическими критериями являются стоимость, которая включает производство, сбор и транспортировку, и количество, которое включает доступность. Существует также вопрос о конкурирующих применениях, таких как производство целлюлозы и картона, сжигание, рециркуляция или рекуперация материалов, а не рекуперация энергии.
7.4.1 Сушка исходного сырья
Обычно для пиролиза требуется сырье с влажностью менее 15%, но существует оптимизация между содержанием влаги и эффективностью процесса конверсии.Фактическое содержание влаги, необходимое для процесса конверсии, очень мало между конверсионными установками. Полученная биомасса обычно имеет влажность в диапазоне 50-60% (влажная масса).
Пассивная сушка во время летнего хранения может снизить это количество примерно до 30 %. Активная сушка силоса позволяет снизить влажность до 12%. Сушка может быть выполнена либо очень простыми средствами, такими как сушка вблизи окружающей среды, солнечная сушка или потоки отходящего тепла, либо с помощью специально разработанных сушилок, работающих на месте.Коммерческие сушилки доступны во многих формах и на разных площадках, но наиболее распространенными являются вращающиеся печи и сушилки с неглубоким псевдоожиженным слоем.
7.4.2 Характеристики исходного сырья
Основные физические характеристики биомассы приведены в Таблице 7.6. Отличительные особенности: довольно высокое содержание влаги, низкая насыпная плотность и широкий диапазон размеров частиц.
Таблица 7.6 Типичные свойства исходного сырья
Сырье | Лесные отходы | дерево процессов | целиком | MSW | Солома |
влажность (% ) | 30-60 | 20-60 | 40-60 | 15-40 | 10-20 |
плотность (кг / м3) | 300 | 350 | 300 | 350 | 200 |
7.4.3 Производство пиролиза, связанное с составом биомассы
Пиролиз древесины приводит к образованию газа, смолы и полукокса (твердого вещества). Конечно, выход этих продуктов напрямую зависит от состава биомассы.
Биомасса состоит из трех основных компонентов: целлюлозы, гемицеллюлозы и лигнина. Целлюлоза представляет собой прямую и жесткую молекулу со степенью полимеризации приблизительно 10.000 единиц глюкозы (сахар C6). Гемицеллюлоза представляет собой полимеры, построенные из сахаров C5, C6 со степенью полимеризации около 200 единиц сахара.И целлюлоза, и гемицеллюлоза могут испаряться с незначительным образованием полукокса при температурах выше 500 ° C. Лигнин представляет собой трехмерный разветвленный полимер, состоящий из фенольных единиц. Из-за ароматического содержания лигнина он медленно разлагается при нагревании и составляет большую часть Образование угля. Помимо основного состава клеточной стенки, такого как целлюлоза, гемицеллюлоза и лигнин, биомасса часто содержит различные количества видов, называемых «экстрактивными веществами». Эти экстрактивные вещества, которые растворимы в полярных или неполярных растворителях, состоят из терпенов, жирных кислот, ароматические соединения и эфирное масло.Состав различных материалов биомассы представлен в таблице 7.7.
Таблица 7.7 Состав различных типов биомассы
Тип | класс | HCL | LIG | Экстра. | ЯСЕНЬ |
Мягкая древесина | 41 | 24 | 28 | 2 | 0.4 |
Твердая древесина | 39 | 35 | 20 | 3 | 0,3 |
Кора сосновая | 34 | 16 | 34 | 14 | 2 |
Солома (пшеница) | 40 | 28 | 17 | 11 | 7 |
Рисовая шелуха | 30 | 25 | 12 | 18 | 16 |
Торф | 10 | 32 | 44 | 11 | 6 |
примечание: CL — целлюлоза; HCL-гемицеллюлоза; LIG-лигнин
Фиг.7.2 показывает процессы, которые управляют пиролизом частиц биомассы. Сначала тепло переносится к поверхности частицы за счет теплопроводности. Нагретый объемный элемент внутри частицы биомассы впоследствии разложился на обугленные и паровые фрагменты, которые состоят из значительных газов (бионефти) и незначительных газов. Из-за объемного образования пара внутри пористой частицы создается давление, которое достигает максимума в центре частицы и уменьшается по направлению к поверхности частицы. Пары, образующиеся внутри пор биомассы, подвергаются дальнейшему растрескиванию, что приводит к образованию полукокса, газов и термически стабильных смол.Длительное время пребывания паров внутри крупных частиц s при низких температурах пиролиза объясняет образование древесного угля в корпусе. Однако этот механизм отсутствует, если размер частиц 1 меньше 1 мм. Когда газообразные продукты покидают частицу биомассы, они попадают в окружающую газовую фазу, где могут разлагаться дальше. Каждый из этих элементарных процессов анализируется ниже с точки зрения свойств частиц, условий процесса и конструкции реактора.
Рис. 7.2. Эскиз разлагающейся древесной частицы, в том числе задействованные пути реакции
Пилотный реактор пиролиза биомассы с вращающимся конусом спроектирован и поставлен Университетом Твенте, Нидерланды.Его производительность 50 кг / час. Вращающийся конус — это реактор нового типа для мгновенного пиролиза биомассы с целью максимального увеличения производства бионефти. Частицы древесины, подаваемые на дно вращающегося конуса вместе с избытком частиц инертного теплоносителя, преобразуются, перемещаясь по спирали вверх вдоль горячей стенки конуса. Геометрия конуса, используемого в работе, определяется верхним углом 90 градусов радиан и максимальным диаметром 650 мм. Наиболее важными преимуществами технологии атмосферного вращающегося конуса являются ее высокая селективность по отношению к бионефти и отсутствие разбавляющего газа.Выход бионефти сопоставим с выходом других технологий производства бионефти.
Отличительными особенностями этого реактора являются: быстрый нагрев (5000 К / с) твердых веществ, короткое время пребывания твердых частиц (0,5 с) и небольшое время пребывания в газовой фазе (0,3 с). Продукты, полученные в результате мгновенного пиролиза древесной пыли во вращающемся конусном реакторе, представляют собой неконденсируемые газы, бионефть (гудрон) и полукокс. Поскольку не требуется газа-носителя (снижение затрат), продукты пиролиза будут образовываться в высоких концентрациях.Если необходимо. уменьшение объема газовой фазы внутри вращающегося конуса возможно за счет перекрытия части объема внутри вращающегося конуса; он сокращает время пребывания газовой фазы в реакторе, за счет чего подавляется крекинг смолы в газовой фазе. На рис. 7.3 показано поперечное сечение реактора, в котором виден вращающийся конус.
Рис. 7.3 Поперечное сечение реактора с вращающимся конусом
Выводы и проблемы
Пиролиз является наиболее универсальной системой конверсии биомассы, предлагает высокие выходы жидких продуктов, которые можно использовать напрямую или модернизировать, эта технология открывает большие перспективы для топлива и химикатов, постоянные исследования и разработки необходимы для реализации потенциала.
Для продуктов с более высокой жидкостью используются более продвинутые процессы в Университете Твенте, Альтене, Ватерлоо, Тюбингенском университете и Исследовательском институте солнечной энергии.
Для интегрированной системы. еще предстоит выполнить следующие работы:
— Сбор данных о процессах производства, сбора, переработки и улучшения биомассы;
— Сбор данных о затратах на транспортировку и обработку биомассы и производных продуктов.
— Продолжение технико-экономических оценочных исследований для оптимизации системы.
— Сделайте установку более дешевой и простой в эксплуатации.
Пиролиз | Энциклопедия
1. ВведениеТермин пиролиз описывает разложение полимеров (, например, смол, целлюлозу), газообразных углеводородов (, например, . Ацетилен) , углеводородных масел и различных других органических материалов, таких как побочные продукты нефти, вызванное исключительно теплом . Газофазный пиролиз ( то есть ., Термический крекинг углеводородов) с последующим осаждением углерода в современной литературе обычно называют химическим осаждением из паровой фазы (CVD) углеродистых материалов. Еще одно хорошо известное применение пиролиза — обработка отходов полимеров (как синтетических, так и природных) для производства биотоплива и биогаза . Здесь температуры термообработки могут быть ниже 900, 90, 347, ° C, и иногда окружающая среда может даже содержать кислород в зависимости от того, что ожидается в качестве конечного продукта.Пиролиз также используется в контексте металлургии (, например, ., в пирометаллургии), где желательным конечным продуктом обычно не является углерод.
Когда органический полимер нагревается выше температуры его разложения, связи углерод-гетероатом начинают расщепляться, за чем следует образование новых связей углерод-углерод. На ранних стадиях пиролиза образуются различные углеводородные радикалы с максимальной концентрацией около 600 o ° C. После 800 o ° C образуется сеть фрагментов графена; содержащий большую долю дефектов, а также химические примеси, начинает развиваться.Дальнейшее нагревание позволяет отжечь дефекты и увеличить размер кристаллитов графена ( L, a ) и толщину стопки ( L, c ). Отсутствие кислорода сводит к минимуму образование CO , 2, и CO (, т.е. ., горение), однако, если в самом полимере присутствует какой-либо (связанный) кислород, образуются некоторые оксиды. Другие продукты пиролиза, такие как CH 4 и небольшие углеводороды, являются летучими и выделяются в виде пузырьков.
Существуют различные теории о механизме образования элементарного углерода из разложившегося полимера. После разложения полимерные фрагменты имеют различные формы и размеры, которые являются подвижными на начальных стадиях пиролиза (500-800 o ° C) и постоянно пытаются достичь термодинамически стабильного расположения путем отделения и слияния с каждым из них. Другой. Различные полимеры демонстрируют различные модели распада и подвижность фрагментов. Например, механизм пиролиза целлюлозы сильно отличается от механизма пиролиза смол.Различные полиимиды, поливинилхлорид, пиридин и др. . имеют свои характерные продукты пиролиза и кинетику реакции. Основные факторы, влияющие на природу образующегося углерода, включают химический состав предшественника, размер структуры, условия нагрева, силы, прилагаемые во время обработки (если таковые имеются), а в случае эпоксидных смол — степень сшивания.
Более подробную информацию о классификации и применении пиролитических углей можно найти здесь [1] .
Теоретические (вычислительные) исследования процесса пиролиза показывают, что первичные фрагменты, образующиеся после разложения полимера, помимо исходной молекулы содержат атомы из соседних цепей. Это открытие подтверждает идею о том, что не существует каких-либо конкретных моделей или четко определенных точек зародышеобразования на начальных стадиях пиролиза и образования углерод-углеродной связи. Тем не менее теоретическими и экспериментальными исследованиями подтверждено, что химический состав полимера играет наиболее важную роль в определении природы образующегося углерода.Следовательно, углеводороды, полученные из полимера, можно разделить в первом приближении на основе природы предшественника.
2. Углерод на основе полимеровКлассификация углерода, полученного из полимера, на основе прекурсоров показана на Рисунке 1, за которым следует краткое объяснение терминологии.
Рисунок 1. Классификация углеродных материалов, полученных пиролизом полимеров. СЭМ изображения: Внизу слева : пиролизованные микростолбы SU-8 с подвешенным волокном SU-8 [65], показывающие коксование, и Внизу справа : часть коры дерева, карбонизированная в результате обугливания.Оба прекурсора подвергаются пиролизу при 900 o ° C со скоростью изменения температуры 5 ° ° C / мин в азотной среде.
2.1. Коксование и обугливание
Если продукт пиролиза (смесь всех промежуточных материалов при любой заданной температуре) проходит через полутвердую (каучукоподобную) фазу из-за того, что его T г падает чуть ниже температуры процесса, это явление известно как коксование. Изображение, полученное с помощью сканирующего электронного микроскопа (SEM) в нижнем левом углу рисунка 1, представляет собой карбонизированную структуру, в которой волокно было намеренно подвешено на массив полых микростолбиков.Можно заметить, что стойки, прикрепленные к волокну, деформируются из-за растяжения волокна во время пиролиза. Другие столбики усаживаются равномерно, что указывает на то, что температура пиролизной смеси T г была лишь немного ниже установленной температуры. По мере увеличения этого зазора узорчатые структуры частично деформируются, и когда он становится значительно большим, в основном получаются маслоподобные материалы. Полутвердый промежуточный материал отвечает за гладкую поверхность образующегося углерода, поскольку он пытается минимизировать его поверхностную энергию.Примерами коксующихся полимеров являются фенолформальдегидные смолы (дает неграфитизирующий углерод) и антрацен (дает графитизирующий углерод).
Обугливание относится к прямому преобразованию жесткой полимерной структуры в углерод, форма которого сохраняется как на макро-, так и на микроскопическом уровне. Дерево и другие целлюлозные полимеры являются хорошими примерами обугливания (см. СЭМ-изображение в правом нижнем углу на Рисунке 1). Главный и наиболее изученный промежуточный продукт, образующийся при пиролизе целлюлозы, известен как левоглюкозан, который далее распадается различными путями, что приводит к образованию смол (маслоподобных материалов), летучих веществ и твердого углерода.Эти фазы обычно сосуществуют и остаются разными на протяжении всего процесса. Твердая углеродная основа воспроизводится в конечном угле, а масла и летучие вещества собираются и при желании перегоняются. Целлюлозные материалы действительно подвергаются некоторому размягчению в области 230-255 o ° C, но это напрямую не коррелирует ни с T g , ни с температурой плавления. Угольки преимущественно не графитизируют и из-за своей пористости и химического состава поверхности часто служат активированным углем.Пиролиз натуральной древесины и других растительных остатков более сложен из-за присутствия лигнина и гемицеллюлозы.
Углеродистые остатки, полученные из биоразлагаемых природных полимеров при температурах <900 o C, часто называют биохарами. Термин полукокс также может иногда обозначать образование твердого углерода из полимеров даже после начального коксования. Важно отметить, что номенклатура углеродных материалов уже полна двусмысленностей из-за существования множества форм углерода (в том числе со смешанной гибридизацией), прекурсоров и производственных процессов.Поэтому следует избегать любой терминологии, которая способствует такой путанице.
2.2. Графитирующий и неграфитизирующий углерод
Графитирующий углерод — это углерод, полученный из полимера, который потенциально может быть преобразован в поликристаллический графит при термообработке, каталитических процессах, нагрузке или любом другом методе. Графит имеет кристаллическую структуру ABABA с разделением слоев 3,354 Å по оси c . На начальных стадиях пиролиза некоторые полукристаллические полимеры, такие как ПВХ, превращаются в углеродистый материал, напоминающий уложенные друг на друга фрагменты графена.Хотя изначально эти фрагменты содержат примеси и имеют турбостратное расположение (беспорядочно повернутые базисные плоскости), их прогрессивное упорядочение при более высоких температурах приводит к образованию графита. Пиролитический графит может быть подвергнут последующей обработке для получения высокоориентированного пиролитического графита (ВОПГ). ВОПГ можно также получить с использованием других методов, таких как перекристаллизация из расплавов железа (коммерчески известная как графит Киша) или термическое сжатие химически осажденного графена.
Неграфитизирующие угли по определению не могут быть преобразованы в кристаллический графит, поскольку они содержат различные структурные дефекты и случайно ориентированные фрагменты графена, демонстрирующие сильную трехмерную связь.Эти турбостратные графеновые фрагменты имеют гауссово распределение по размеру и форме, длине связи C-C и углам валанса, а также имеют межслоевое разделение> 0,335 нм. Наличие дефектов заставляет эти фрагменты скручиваться и складываться и образовывать фуллереноподобные структуры, а иногда и полностью закрытые бакминстерфуллерены. Изогнутые структуры сосуществуют с более крупными, сложенными друг на друга листами графена. Неграфитизированный уголь демонстрирует более низкую электропроводность, но более высокую твердость по сравнению с графитом, и его также называют твердым углеродом.Смолы PF, целлюлоза, поливинилиденхлорид и некоторые полиимиды дают неграфитизирующий углерод при пиролизе.
2.3. Стекловидный (стекловидный) и активированный уголь
Неграфитизированный углерод высокой чистоты, который подвергся по крайней мере некоторому закоксовыванию во время пиролиза, известен как стеклоуглерод. В случае крупномасштабных (миллиметровых) структур стеклоуглерод получается при температуре> 2000 90 347 o ° C, поскольку промежуточные продукты пиролиза могут проявлять плохую теплопроводность, вызывая температурный градиент в образце.Эти повышенные температуры необходимы для систематического отжига летучих компонентов и обеспечения чистоты до центра структуры. Показано, что в некоторых промышленных процессах получение стеклоуглерода происходит при 1000 90 347 o 90 350 ° C с модифицированными условиями пиролиза для размеров конструкции ≤ 3 мм. Несколько исследований подтвердили, что в случае структур микро / наноразмеров свойства стеклоуглерода могут быть достигнуты при более низких температурах, таких как 900 o ° C, вероятно, с некоторыми примесью кислорода.
Активированный уголь — это неграфитизирующий уголь, образованный прямым обугливанием, который содержит поверхностные радикалы и открытые поры. У них есть гетероатомы и больше дефектов по сравнению со стеклоуглеродом, а их электропроводность и механическая прочность обычно ниже. Благодаря активному химическому составу поверхности они часто используются в качестве адсорбентов и каталитических слоев.
2.4. Углеродные волокна
Микро- и наноразмерные волокна, полученные пиролизом целлюлозы, полиакрилонитрила (ПАН) или других полимерных волокон, традиционно не классифицировались как стеклообразные или активированные на основе химического состава прекурсора.Картина отжига в волокнах значительно отличается от объема из-за высокого отношения поверхности к объему. Обработка поверхности, параметры изготовления и, в случае ПАН, предпиролизное окисление могут сильно повлиять на их свойства. Сообщалось, что волокна имеют тенденцию становиться более упорядоченными (графитовыми), если процесс изготовления (обычно электропрядение) модифицируется, вводятся добавки или возникает напряжение.
Запись от 10.3390 / ma11101857
PYROLYSIS
Нагревание органических материалов в отсутствие воздуха / кислорода вызывает химические и физические изменения.Самый старый из инженеров-химиков, производитель древесного угля , сложил свои дрова в насыпи, покрытые грязью и нагретые («сожженные») в условиях относительного отсутствия воздуха. Вырубка лесов в северо-западной Европе и Британии, которая достигла своего апогея во время роста населения в XI-XII веках, как полагают, была произведена рукой самого угольщика. Серьезные последствия аналогичного обезлесения сегодня ощущаются в некоторых частях Африки и Азии.Пиролиз древесины выделяет легкие газы, такие как оксид углерода и диоксид углерода, легких спиртов, альдегидов, кетонов и органических кислот. Смолы — это летучие продукты пиролиза древесины с большей молекулярной массой, которые легко конденсируются при температуре окружающей среды. С гораздо более высоким содержанием углерода, чем в исходной древесине (40-50% углерода против 75-90% углерода), и почти ничтожным содержанием серы, твердый остаток («полукокс», «древесный уголь») традиционно был ценным топливом для аграрные сообщества. Раннее производство стали в 15-17 веках в Европе, включая в конечном итоге успешные попытки отливки стальных ружей под руководством Генриха VIII, основывалось на восстановлении оксидов железа углеродом в древесном угле; Производство стали с использованием древесного угля, в настоящее время основанное на выращивании древесного угля из эвкалипта в современной Бразилии, по-видимому, экономически выживает из-за низкой структуры заработной платы.
Для сохранения хороших свойств воспламенения в качестве домашнего топлива древесный уголь должен сохранять некоторое (около 10%) исходное содержание летучих веществ; следовательно, температуры при этом типе пиролиза редко превышают 400-450 ° C. Как и во всех пиролитических процессах, первичные продукты термического разложения древесины являются реактивными: термический разрыв связей приводит к образованию широкого спектра свободных радикалов. Свободные радикалы меньшего размера обладают высокой реакционной способностью, с нано- или микросекундными периодами полураспада, в то время как свободные радикалы большего размера, такие как свободный радикал трифенилметил, химически стабильны в растворе.Таким образом, распределение конечных продуктов пиролитических процессов в значительной степени зависит от таких параметров реакции, как температура, давление, время пребывания летучих веществ в нагретой зоне и степень контакта паров смолы с нагретыми твердыми поверхностями. Не имея доступа к нашей терминологии, традиционный производитель древесного угля, тем не менее, сложил древесину высоко, чтобы продлить путь эволюционирующих смол, чтобы обеспечить максимальную повторную конденсацию смол и образование вторичного обугливания. Ожидаемое распределение продуктов при медленном пиролизе будет включать 15-30% полукокса и 35-45% смол и жидкостей (включая водную фазу), а остальная часть выделяется в виде газов.
Уже не считающаяся экономичной или экологически приемлемой, «разрушающая перегонка древесины» до последних 60 лет была основным источником химического сырья, такого как метанол (древесный спирт), ацетон, уксусная кислота и смолы. Последний исторически часто использовался в качестве изоляции от проникновения воды или влаги на такие разные конструкции, как крыши и внешние стены домов и деревянные корпуса кораблей и лодок. «Стокгольмский деготь» по-прежнему широко продается в Великобритании для аналогичных повседневных применений в домашних условиях и для использования в качестве антисептиков при уходе за лошадьми.Совсем недавно пиролиз сельскохозяйственных и лесных отходов и твердых бытовых отходов был изучен как вероятный технологический путь для удаления отходов и производства энергетического и химического сырья. Хотя некоторые из этих термохимических процессов активно исследуются, их применение в промышленном масштабе еще не появилось. Для недавнего обзора термохимической обработки биомассы см. Bridgewater (1994).
Наиболее широкое прямое промышленное применение пиролиза в настоящее время находится в работе коксовой печи .Он заключается в нагревании угля в ячеистых печах, которые могут быть шириной 0,60–1 м, длиной до 15 м и высотой нескольких метров. Конструкция коксовой печи и условия реакции (например, температуры) могут быть изменены для изменения распределения продуктов в соответствии со структурой спроса и цен. В Европе 1840-х годов уголь «карбонизация» использовался для производства газа для отопления и освещения домов; Изначально только королевские дворцы и аналогичные дома могли воспользоваться этим новым продуктом «науки».Повышение спроса на ароматических химикатов (например, толуол для взрывчатых веществ, нафталин для шариков от моли) в первые десятилетия 20-го века превратило смолы в основной продукт. Внутреннее использование угольного газа в Великобритании прекратилось с повсеместным распределением природного газа из Северного моря в начале 1970-х годов. Во второй половине века кокс для металлургии, особенно для производства стали, вышел на первый план. Отсутствие рынков и действующее законодательство о загрязнении привело к использованию газа и побочных продуктов в качестве топлива для коксовых печей.
Когда бытовым газом был желаемый продукт, температура печи достигала бы максимум 850 ° C, и полученный кокс считался желательным домашним топливом; время реакции составляло 7-8,5 часов. До 45% газа можно ожидать от хорошего газа — угля, горючие компоненты газа состоят из метана, , окиси углерода и водорода. В то время как во время нагревания из битуминозного угля среднего сорта может выделяться от 22 до 30% смолы, интенсивные вторичные реакции с добавлением частиц в коксовых печах обычно снижают выход смолы до 5-10% от веса исходного угля.Если требуется кокс металлургического сорта , температура печи может быть повышена до 1100-1200 ° C, а время реакции увеличивается до 10-14 часов. Твердость и сопротивление разрушению образующегося кокса являются критическими характеристиками при работе доменной печи. Более высокие выходы гудрона, близкие к количествам, первоначально выделенным из частиц угля, могут быть получены за счет снижения температуры и времени пребывания летучих веществ в зоне реакции. В 1930-х годах была предпринята попытка «низкотемпературной карбонизации» в качестве технологического маршрута для получения более высоких выходов жидких продуктов пиролиза угля: использовалось множество конфигураций реакторов, от аналогов коксовых печей до псевдоожиженных слоев.До начала Второй мировой войны эти попытки были экономически неудачными, в основном из-за более низкой цены на мазут, полученный из нефти. Нехватка нефти в годы войны дала новый импульс развитию ряда угольных отраслей промышленности, особенно в Германии и Японии, где технологии низкотемпературной карбонизации были сохранены и расширены, включая переработку гудрона и вторичную переработку. Имеется обширная литература по теме коксования / карбонизации и хорошие обзоры [Lowry (1963) и Elliott (1980)].
Термин пиролиз также охватывает термохимическую обработку жидких и газообразных веществ, обычно для образования более мелких молекул путем крекинга. Большие объемы этилена производятся из такого разнообразного сырья, как метан, этан, нефтяная нафта, легкий газ и жидкое топливо. Эти процессы обычно проводят при давлении от 1 до 30 бар и температуре от 700 до 1200 ° C в длинных (20-30 метров) тонких (1-2 дюйма) реакторных трубах, изготовленных из тугоплавких сплавов, с внешним обогревом.Первоначальные реакции в этих процессах включают разрыв ковалентной связи с высвобождением очень активных свободных радикалов. Схемы реакций, включающие первичные, вторичные и т. Д. Продукты, считаются очень сложными, и широкий спектр продуктов (от легкого газа до смолы и кокса) может образоваться в результате крекинга такого простого газа, как чистый этан. В промышленном масштабе распределение продуктов регулируется путем манипулирования параметрами процесса, включая время пребывания в зоне нагрева, и введением разбавителей с минимальной реакционной способностью, таких как пар, или инертных разбавителей, таких как азот.Желаемое время контакта может составлять всего несколько миллисекунд, а устройства быстрой закалки в промышленном масштабе часто имеют элегантную конструкцию. Многие промышленно важные реакции выполняются в таких реакторах пиролиза (с соотношением длина / диаметр, которое может составлять всего 10-12), что приводит к производству сыпучих химикатов, таких как VCM (мономер винилхлорида) и специальных химикатов, таких как тетрафторэтилен. [Albright et al. (1983)].
Пиролитические процессы, включающие выделение летучих веществ (газов и смол) и образование нагара, представляют собой начальную (или промежуточную) стадию во многих общепромышленных применениях, например.г., сжигание пылевидного угля. При пиролизе угля ожидается, что температура, давление и скорость нагрева на стадии пиролиза будут влиять на
распределение продукта (газ-гудрон-уголь),
структурные особенности смол-продуктов,
реакционная способность обугленных, образующихся при пиролизе.
Считается, что последняя реактивность важна при попытке решить такие широкие проблемы, как подавление содержания углерода в летучей золе (в камерах сгорания ПТ) и оценка производительности газификаторов угля с псевдоожиженным слоем и камер сгорания нового поколения вместе взятых. системы циклической выработки электроэнергии.
Исследование пиролитического поведения твердых тел требует тщательного планирования экспериментов. Например, из-за реакционной природы продуктов мелкий и глубокий реакторы с неподвижным слоем не будут давать одинакового распределения продукта: сравнение выходов, полученных в лабораторных экспериментальных реакторах разной конфигурации, показало, что выходы смол можно повысить почти на 50. %, если смолы извлекаются при относительном отсутствии вторичных реакций вне частиц. Типы аппаратов, используемых для этих целей, варьируются от реакторов с неподвижным слоем и псевдоожиженным слоем, где летучие вещества могут находиться относительно долгое время в нагретой зоне, до реакторов с увлеченным потоком («капельная труба»), где летучие вещества продукта проходят по всей длине нагретой зоны. трубка реактора и реакторы с проволочной сеткой, где монослой образца удерживается между сложенными слоями сетки, натянутой между парой электродов, причем сетка также действует как резистивный нагреватель.В случае применения реактора с проволочной сеткой, если летучие вещества уносятся из области сетки в зону гашения, конфигурация реактора позволяет летучим компонентам относительно быстро очищать неглубокую нагретую реакционную секцию (менее 1 мм) [Gonenc et al. (1990)]. Образцы смолы, извлеченные в аппарате этого типа, будут небольшими (1-2 мг), но можно ожидать, что они будут иметь структурные особенности, относительно мало измененные по сравнению с парами смолы, выделяемыми пиролизирующими частицами угля.